Beherrschung von CNC-Maschinen: Den entscheidenden Unterschied zwischen Vorschubgeschwindigkeit und Spindeldrehzahl verstehen
Inhaltsverzeichnis
1. Was ist Schnittgeschwindigkeit bei der CNC-Bearbeitung?
Die Schnittgeschwindigkeit ist ein grundlegender Begriff bei der CNC-Bearbeitung und stellt die Oberflächengeschwindigkeit dar, mit der das Schneidwerkzeug am Werkstück vorbeibewegt. Sie wird normalerweise in Oberflächenfuß pro Minute (SFM) oder Metern pro Minute gemessen. Im Wesentlichen ist die Schnittgeschwindigkeit die Geschwindigkeit, mit der die Schneide des Werkzeugs das zu schneidende Material durchquert.
Dieser Parameter ist von entscheidender Bedeutung, da er die Effizienz des Schneidvorgangs und die Qualität der fertigen Oberfläche direkt beeinflusst. Ein Beispiel für eine Komponente, die bei der Schneidgeschwindigkeit eine Rolle spielt, ist die Omron PLC.
Diese SPS können die Geschwindigkeit verschiedener Komponenten einer CNC-Maschine steuern und so ein gleichmäßiges und präzises Schneiden gewährleisten. Weitere Informationen zu diesem und anderen Produkten finden Sie auf der Omron SPS Seite.
Stellen Sie sich einen Drehvorgang vor, bei dem ein zylindrisches Werkstück gedreht wird. Die Schnittgeschwindigkeit ist die Geschwindigkeit, mit der sich das Schneidwerkzeug während einer Spindelumdrehung entlang des Umfangs des Werkstücks bewegt.
Die Berechnung umfasst den Durchmesser des Werkstücks und die Drehzahl der Spindel (U/min). Hohe Schnittgeschwindigkeiten können zu einem schnelleren Materialabtrag führen, können aber auch zu erhöhtem Werkzeugverschleiß führen.
Daher ist die Wahl der optimalen Schnittgeschwindigkeit ein Balanceakt zwischen Produktivität und Werkzeuglebensdauer. Die Fähigkeiten der Maschine, das Werkzeugmaterial und das Werkstückmaterial spielen bei der Bestimmung der geeigneten Schnittgeschwindigkeit eine entscheidende Rolle.
2. Wie unterscheidet sich die Spindeldrehzahl von der Schnittgeschwindigkeit?
Obwohl sie oft synonym verwendet werden, sind Spindeldrehzahl und Schnittgeschwindigkeit unterschiedliche, aber dennoch miteinander verbundene Konzepte. Die Spindeldrehzahl bezieht sich auf die Drehgeschwindigkeit der Maschinenspindel, gemessen in Umdrehungen pro Minute (U/min).
Es handelt sich um die Geschwindigkeit, mit der sich die Spindel dreht, die entweder das Werkstück (bei einer Drehbank) oder das Schneidwerkzeug (bei einer Fräse) hält. Die Schnittgeschwindigkeit hingegen ist, wie zuvor definiert, die Oberflächengeschwindigkeit des Schneidwerkzeugs relativ zum Werkstück.
Die Beziehung zwischen Schnittgeschwindigkeit und Spindeldrehzahl kann als einfache Formel visualisiert werden: Spindeldrehzahl (U/min) = (Schnittgeschwindigkeit (SFM) * 3,82) / Werkzeugdurchmesser.
Diese Formel verdeutlicht, dass bei einer bestimmten Schnittgeschwindigkeit die Spindeldrehzahl an den Durchmesser des Schneidwerkzeugs oder Werkstücks angepasst werden muss. Beispielsweise erfordert ein kleinerer Werkzeugdurchmesser eine höhere Spindeldrehzahl, um die gleiche Schnittgeschwindigkeit wie ein größeres Werkzeug zu erreichen.
Ein tiefes Verständnis des Unterschieds ist für CNC-Programmierer und -Maschinisten entscheidend, um eine präzise Bearbeitung zu gewährleisten. Wenn Sie neugierig auf verschiedene CNC-Werkzeuge und deren Beziehung zur Spindeldrehzahl sind, erkunden Sie Ressourcen wie Mitsubishi PLC kann wertvolle Erkenntnisse liefern.
3. Was genau ist die Vorschubgeschwindigkeit bei der CNC-Bearbeitung?
Die Vorschubgeschwindigkeit bei der CNC-Bearbeitung ist die Geschwindigkeit, mit der sich das Schneidwerkzeug oder das Werkstück während des Schneidvorgangs relativ zueinander entlang einer bestimmten Achse bewegt. Einfacher ausgedrückt: Es geht darum, wie schnell sich das Werkzeug durch das zu schneidende Material bewegt.
Die Vorschubgeschwindigkeit wird normalerweise in Einheiten von Distanz pro Umdrehung (z. B. Zoll pro Umdrehung) oder Distanz pro Minute (z. B. Zoll pro Minute) gemessen. Dies ist ein kritischer Parameter, der die Spanbelastung des Werkzeugs beeinflusst.
Bei einem Fräsvorgang beispielsweise bestimmt die Vorschubgeschwindigkeit, wie schnell der Fräser bei jeder Spindelumdrehung in das Werkstück eindringt. Bei einem Drehvorgang bestimmt sie, wie weit sich das Werkzeug bei jeder Spindelumdrehung entlang der Länge des Werkstücks bewegt.
Die Vorschubgeschwindigkeit muss sorgfältig anhand des Werkzeugmaterials, des Werkstückmaterials, der Schnitttiefe und der gewünschten Oberflächengüte ausgewählt werden. Eine falsch gewählte Vorschubgeschwindigkeit kann zu Problemen wie schlechter Oberflächenqualität, Werkzeugbruch oder übermäßigem Werkzeugverschleiß führen. Erfahren Sie mehr über HMI, eine Komponente, die eine wesentliche Rolle bei der Steuerung der Vorschubgeschwindigkeit spielt, auf der Bediengerät Seite.
4. Welchen Einfluss hat die Vorschubgeschwindigkeit auf den Bearbeitungsprozess?
Die Vorschubgeschwindigkeit hat erhebliche Auswirkungen auf verschiedene Aspekte des Bearbeitungsprozesses, darunter Standzeit, Oberflächengüte, Spanbildung und allgemeine Bearbeitungseffizienz. Eine höhere Vorschubgeschwindigkeit bedeutet im Allgemeinen einen schnelleren Materialabtrag, was zu einer höheren Produktivität führt.
Allerdings führt dies auch zu einer höheren Spanlast, also der Dicke des Materials, das von jeder Schneide des Werkzeugs bei einer Umdrehung abgetragen wird. Dies kann zu erhöhten Schnittkräften und Wärmeentwicklung führen und bei unsachgemäßer Handhabung möglicherweise zu beschleunigtem Werkzeugverschleiß oder sogar zu Werkzeugbrüchen führen.
Umgekehrt verringert eine geringere Vorschubgeschwindigkeit die Spanlast, was zu einer besseren Oberflächengüte und potenziell einer längeren Werkzeuglebensdauer führt. Allerdings verringert sich dadurch auch die Materialabtragsrate, was längere Zykluszeiten und eine geringere Produktivität zur Folge hat.
Das Finden der optimalen Vorschubgeschwindigkeit ist ein heikler Balanceakt, der eine sorgfältige Berücksichtigung des jeweiligen Bearbeitungsvorgangs, des Werkzeugmaterials, des Werkstückmaterials und des gewünschten Ergebnisses erfordert. Maschinisten und CNC-Programmierer konsultieren häufig Vorschub- und Geschwindigkeitstabellen und nutzen ihre Erfahrung, um die geeignete Vorschubgeschwindigkeit für eine bestimmte Aufgabe zu bestimmen.
Eine Schneider-SPS ist ein Beispiel für ein System, das so programmiert werden kann, dass es die Vorschubgeschwindigkeit dynamisch anpasst und so den Bearbeitungsprozess optimiert. Die gesamte Produktpalette finden Sie hier Schneider PLC.
5. Welche Beziehung besteht zwischen Schnittgeschwindigkeit und Vorschub?
Schnittgeschwindigkeit und Vorschubgeschwindigkeit sind miteinander verknüpfte Parameter, die gemeinsam berücksichtigt werden müssen, um den CNC-Bearbeitungsprozess zu optimieren. Sie wirken sich direkt aufeinander aus und bestimmen gemeinsam die Spanlast, die Materialabtragsrate, die Werkzeuglebensdauer und die Oberflächengüte. Das Verständnis dieser Beziehung ist für jeden Maschinisten oder CNC-Programmierer von entscheidender Bedeutung.
Parameter | Beziehung zur Schnittgeschwindigkeit | Beziehung zur Vorschubgeschwindigkeit |
---|---|---|
Chip-Ladung | Steigt mit geringerer Schnittgeschwindigkeit (bei konstantem Vorschub) | Steigt mit höherem Vorschub (bei konstanter Schnittgeschwindigkeit) |
Materialabtragsrate | Steigt mit höherer Schnittgeschwindigkeit | Steigt mit höherem Vorschub |
Standzeit | Generell sinkt mit höherer Schnittgeschwindigkeit | Kann bei zu hohem oder zu niedrigem Vorschub abnehmen |
Oberflächenfinish | Kann sowohl durch Schnittgeschwindigkeit als auch durch Vorschub beeinflusst werden | Verbessert sich im Allgemeinen bei niedrigerer Vorschubgeschwindigkeit (bei konstanter Geschwindigkeit) |
Schnittkräfte | Generell mit höherer Schnittgeschwindigkeit und Vorschubgeschwindigkeit zunehmen | Generell mit höherem Vorschub ansteigend |
Wärmeerzeugung | Steigt mit höherer Schnittgeschwindigkeit und Vorschubgeschwindigkeit | Steigt mit höherem Vorschub |
Bearbeitungszeit | Nimmt mit höherer Schnittgeschwindigkeit und Vorschubgeschwindigkeit ab | Nimmt mit zunehmender Vorschubgeschwindigkeit ab |
Spindellast | Steigt mit höherer Schnittgeschwindigkeit (bei konstantem Vorschub) | Steigt mit zunehmender Vorschubgeschwindigkeit (bei konstanter Drehzahl) |
Maschinenleistung | Direkt proportional zur Schnittgeschwindigkeit und Vorschubgeschwindigkeit | Direkt proportional zur Vorschubgeschwindigkeit |
Fräserablenkung | Kann mit höherem Vorschub, insbesondere bei kleinen Fräsern, gesteigert werden | Steigt mit höherem Vorschub |
Im Wesentlichen führt eine Erhöhung der Schnittgeschwindigkeit bei gleichbleibender Vorschubgeschwindigkeit zu einer geringeren Spanlast, aber einem höheren Materialabtrag. Umgekehrt führt eine Erhöhung der Vorschubgeschwindigkeit bei gleichbleibender Schnittgeschwindigkeit zu einer größeren Spanlast und ebenfalls einem höheren Materialabtrag.
Der Maschinist muss das richtige Gleichgewicht zwischen diesen beiden Parametern finden, um die gewünschten Ergebnisse zu erzielen, ohne dabei Kompromisse bei der Werkzeuglebensdauer oder Oberflächenqualität einzugehen. Mithilfe eines Proface HMI können Bediener diese Parameter beispielsweise in Echtzeit überwachen und anpassen, um eine optimale Leistung sicherzustellen. Weitere Informationen zu diesen HMIs finden Sie hier Proface HMI.
6. Wie berechnen Sie die optimale Schnittgeschwindigkeit und Vorschubrate?
Die Berechnung der optimalen Schnittgeschwindigkeit und des optimalen Vorschubs erfordert eine Kombination aus theoretischen Berechnungen, empirischen Daten und praktischer Erfahrung.
Hersteller von Schneidwerkzeugen geben häufig empfohlene Schnittparameter (Schnittgeschwindigkeit und Vorschub pro Zahn) für ihre Werkzeuge an, die auf dem Werkstückmaterial und dem Werkzeugmaterial basieren. Diese Empfehlungen dienen als guter Ausgangspunkt für die Bestimmung der Anfangseinstellungen.
Die Grundformel zur Berechnung der Spindeldrehzahl (RPM) basierend auf der Schnittgeschwindigkeit (SFM) und dem Werkzeugdurchmesser lautet:
RPM = (Schnittgeschwindigkeit (SFM) * 3,82) / Werkzeugdurchmesser
Sobald die Spindeldrehzahl bestimmt ist, kann die Vorschubgeschwindigkeit mithilfe des Vorschubs pro Zahn und der Anzahl der Zähne am Fräser berechnet werden:
Vorschubgeschwindigkeit (IPM) = U/min * Anzahl der Zähne * Vorschub pro Zahn
Diese Berechnungen stellen jedoch nur einen Ausgangspunkt dar. Die tatsächlich optimale Schnittgeschwindigkeit und Vorschubrate können je nach Faktoren wie Maschinensteifigkeit, Schnitttiefe (axiale und radiale Tiefe), Werkzeugverschleiß und gewünschter Oberflächengüte variieren.
Erfahrene Maschinisten optimieren diese Parameter häufig auf der Grundlage ihrer Beobachtungen des Schneidprozesses, wie z. B. Spanbildung, Schnittkräfte und Werkzeugzustand. Wenn Sie eine erweiterte Kontrolle benötigen, erkunden Sie Optionen wie Servo Systeme können die für die Feinabstimmung dieser Parameter erforderliche Präzision bieten.
7. Warum sind Spindeldrehzahl und Vorschubgeschwindigkeit entscheidend für die Werkzeuglebensdauer?
Spindeldrehzahl und Vorschubgeschwindigkeit bestimmen die Werkzeuglebensdauer ausschlaggebend. Falsch eingestellte Parameter können zu vorzeitigem Werkzeugverschleiß, Werkzeugbruch oder sogar zu Schäden an der Werkzeugmaschine selbst führen. Das Verständnis, wie sich diese Parameter auf die Werkzeuglebensdauer auswirken, ist für eine kostengünstige und effiziente Bearbeitung unerlässlich.
Zu hohe Schnittgeschwindigkeiten können übermäßige Hitze erzeugen und zu schnellem Werkzeugverschleiß führen, insbesondere an der Schneide des Werkzeugs. Dies liegt daran, dass die Relativgeschwindigkeit zwischen Schneidwerkzeug und Werkstück hoch ist und dadurch eine erhöhte Reibung entsteht.
Andererseits kann ein zu hoher Vorschub zu übermäßigen Spanbelastungen führen, was zu Absplitterungen oder Brüchen der Schneide führt. Umgekehrt kann ein zu niedriger Vorschub Reibung statt Schneiden verursachen, was zu Hitzestau und Werkzeugverschleiß führt.
8. Welchen Einfluss haben unterschiedliche Materialien auf Schnittgeschwindigkeit und Vorschub?
Das zu bearbeitende Material beeinflusst maßgeblich die Wahl der Schnittgeschwindigkeit und des Vorschubs. Unterschiedliche Materialien weisen unterschiedliche Härtegrade, Zähigkeit und Abrasivität auf, die sich direkt auf den Schneidprozess auswirken.
Beispielsweise können weichere Materialien wie Aluminium im Allgemeinen mit höheren Schnittgeschwindigkeiten und Vorschubgeschwindigkeiten bearbeitet werden als härtere Materialien wie Edelstahl.
Dies liegt daran, dass weichere Materialien bei der Bearbeitung weniger Wärme und Schnittkräfte erzeugen. Härtere Materialien erfordern dagegen geringere Schnittgeschwindigkeiten, um übermäßige Wärmeentwicklung und Werkzeugverschleiß zu vermeiden.
Hier ist eine vereinfachte Tabelle, die die empfohlenen Schnittgeschwindigkeiten (SFM) für verschiedene Materialien bei Verwendung von Schnellarbeitsstahlwerkzeugen veranschaulicht:
Material | Schnittgeschwindigkeit (SFM) |
---|---|
Aluminium | 300-1000 |
Messing | 200-500 |
Weichstahl | 80-150 |
Edelstahl | 40-80 |
Titan | 30-60 |
Gusseisen | 60-120 |
Kunststoffe | 100-300 |
Kupfer | 150-400 |
Bronze | 100-250 |
Gehärteter Stahl | 20-40 |
Nickellegierungen | 25-50 |
Verbundwerkstoffe | 50-150 |
Holz | 500-1500 |
Acryl | 200-600 |
Polycarbonat | 150-450 |
Die Vorschubgeschwindigkeit ist auch materialabhängig. Härtere Materialien erfordern möglicherweise einen geringeren Vorschub pro Zahn, um einen Werkzeugbruch zu vermeiden, während weichere Materialien einen höheren Vorschub pro Zahn vertragen.
9. Welche Fehler treten häufig beim Einstellen der Vorschub- und Geschwindigkeitsparameter auf?
Beim Einstellen der Vorschub- und Geschwindigkeitsparameter bei der CNC-Bearbeitung können mehrere häufige Fehler auftreten. Ein häufiger Fehler besteht darin, sich ausschließlich auf theoretische Berechnungen zu verlassen, ohne die spezifischen Eigenschaften von Maschine, Werkzeug und Werkstück zu berücksichtigen. Dies kann zu suboptimalen Schnittbedingungen und verringerter Effizienz führen.
Ein weiterer häufiger Fehler ist die Nichtbeachtung der Höchstgeschwindigkeits- und Leistungsbeschränkungen der Maschine. Der Versuch, eine Maschine mit Geschwindigkeiten und Vorschüben zu betreiben, die ihre Leistungsfähigkeit überschreiten, kann zu schlechter Leistung, Werkzeugschäden oder sogar Maschinenschäden führen.
Darüber hinaus kann das Ignorieren der Empfehlungen des Werkzeugherstellers hinsichtlich der Schnittparameter zu einem vorzeitigen Werkzeugausfall führen.
Ein weiterer häufiger Fehler ist, dass Vorschub und Geschwindigkeit nicht an die Schnitttiefe angepasst werden. Ein tieferer Schnitt erfordert im Allgemeinen eine Reduzierung von Schnittgeschwindigkeit und Vorschub, um die Lebensdauer des Werkzeugs zu erhalten und Werkzeugbrüche zu vermeiden.
Schließlich kann es zu Ineffizienzen führen, wenn der Schneidvorgang nicht überwacht wird und keine erforderlichen Anpassungen vorgenommen werden. Erfahrene Maschinisten beobachten ständig Faktoren wie Spanbildung, Schnittkräfte und Oberflächenbeschaffenheit, um die Parameter während des Betriebs zu optimieren.
10. Welche fortschrittlichen Techniken können die Effizienz der CNC-Bearbeitung optimieren?
Mehrere fortschrittliche Techniken können die Effizienz der CNC-Bearbeitung über die Grundprinzipien von Schnittgeschwindigkeit und Vorschub hinaus weiter optimieren. Eine solche Technik ist die Steuerung der konstanten Oberflächengeschwindigkeit (CSS), die insbesondere bei Dreharbeiten nützlich ist.
CSS passt die Spindeldrehzahl (U/min) automatisch an, wenn sich das Werkzeug über verschiedene Durchmesser des Werkstücks bewegt, und sorgt so für eine konstante Schnittgeschwindigkeit. Dies gewährleistet gleichmäßigen Werkzeugverschleiß und eine gleichmäßige Oberflächengüte am gesamten Werkstück.
Die Hochgeschwindigkeitsbearbeitung (HSM) ist eine weitere fortschrittliche Technik, bei der hohe Spindeldrehzahlen, hohe Vorschubgeschwindigkeiten und geringe Schnitttiefen genutzt werden, um hohe Materialabtragsraten bei gleichzeitig hervorragender Oberflächengüte und Genauigkeit zu erzielen. HSM erfordert starre Maschinen, spezielle Schneidwerkzeuge und fortschrittliche CNC-Programmiertechniken.
Die adaptive Steuerung ist eine hochmoderne Technologie, die Sensoren verwendet, um den Schneidvorgang in Echtzeit zu überwachen und die Vorschub- und Geschwindigkeitsparameter automatisch anzupassen, um die Leistung zu optimieren. Dadurch können Schwankungen in der Materialhärte, Werkzeugverschleiß und andere Faktoren ausgeglichen werden, die den Bearbeitungsprozess beeinträchtigen können.
Häufig gestellte Fragen
Die Schnittgeschwindigkeit bezeichnet die Oberflächengeschwindigkeit, mit der das Schneidwerkzeug am Werkstück vorbeibewegt. Sie wird normalerweise in Fuß pro Minute (SFM) oder Metern pro Minute gemessen. Die Spindeldrehzahl hingegen ist die Rotationsgeschwindigkeit der Maschinenspindel in Umdrehungen pro Minute (RPM).
Die Vorschubgeschwindigkeit beeinflusst direkt die Spanlast. Eine höhere Vorschubgeschwindigkeit führt zu einer größeren Spanlast, d. h. jede Schneide des Werkzeugs entfernt pro Umdrehung einen dickeren Materialspan. Umgekehrt verringert eine niedrigere Vorschubgeschwindigkeit die Spanlast.
Schnittgeschwindigkeit und Vorschub sind voneinander abhängige Parameter, die gemeinsam die Materialabtragsrate, die Standzeit des Werkzeugs, die Oberflächengüte und die Gesamteffizienz des Bearbeitungsprozesses bestimmen. Um optimale Ergebnisse zu erzielen, müssen sie gemeinsam berücksichtigt werden.
Zu hohe Schnittgeschwindigkeiten können übermäßige Hitze erzeugen, was zu schnellem Werkzeugverschleiß, Werkzeugverformung oder sogar Werkzeugversagen führen kann. Auch die Oberflächengüte des Werkstücks kann dadurch beeinträchtigt werden.
Verschiedene Werkzeugmaterialien weisen unterschiedliche Härte- und Hitzebeständigkeitsgrade auf, was sich auf die empfohlenen Schnittgeschwindigkeiten auswirkt. Beispielsweise können Hartmetallwerkzeuge im Allgemeinen höheren Schnittgeschwindigkeiten standhalten als Schnellarbeitsstahlwerkzeuge.
Versorgen Sie Ihre Projekte mit brandneuen, originalen Servos von Omron, Mitsubishi und Schneider – auf Lager, sofort verfügbar!
Abschluss
- Schnittgeschwindigkeit und Vorschub sind grundlegende Parameter bei der CNC-Bearbeitung.
- Die Spindeldrehzahl unterscheidet sich von der Schnittgeschwindigkeit, steht aber in direktem Zusammenhang.
- Die Vorschubgeschwindigkeit hat erhebliche Auswirkungen auf die Standzeit des Werkzeugs, die Oberflächengüte und die Bearbeitungseffizienz.
- Optimale Schnittgeschwindigkeit und Vorschubrate hängen vom Werkzeugmaterial, Werkstückmaterial, Maschinenfunktionen und dem gewünschten Ergebnis ab.
- Unterschiedliche Materialien erfordern unterschiedliche Schnittparameter.
- Zu den häufigsten Fehlern zählen das Nichtbeachten von Maschinenbeschränkungen, das Ignorieren von Werkzeugempfehlungen und das Versäumnis, Parameter basierend auf der Schnitttiefe anzupassen.
- Fortschrittliche Techniken wie konstante Oberflächengeschwindigkeit, Hochgeschwindigkeitsbearbeitung und adaptive Steuerung können die Effizienz der CNC-Bearbeitung weiter optimieren.
- Für optimale Ergebnisse sind eine kontinuierliche Überwachung und Anpassung der Parameter von entscheidender Bedeutung.
- Erfahrung und ein tiefes Verständnis der besprochenen Prinzipien sind für jeden erfolgreichen CNC-Maschinisten oder -Programmierer von entscheidender Bedeutung.
- Die Wahl der richtigen Lieferanten wie Mitsubishi Servo oder Omron Wechselrichter kann Ihre Bearbeitungsmöglichkeiten erheblich verbessern.
Kontaktieren Sie uns
Geben Sie in dieses Formular einfach Ihren Namen, Ihre E-Mail-Adresse und eine kurze Beschreibung Ihrer Anfrage ein. Wir werden Sie innerhalb von 24 Stunden kontaktieren.
Diese Themen könnten Sie auch interessieren
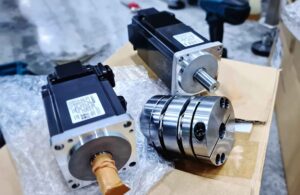
Kanadas Top 5 Mitsubishi Servo-Lieferanten
Als engagierter Ingenieur bei Kwoco habe ich jahrelang Erfahrung im Bereich der industriellen Automatisierung. Meine Erfahrung mit international renommierten Marken wie Mitsubishi hat mir das Wissen vermittelt, die besten Lieferanten auf dem Markt zu identifizieren.
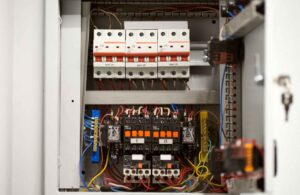
Was ist ein Schaltschrank? Wichtige Erkenntnisse erklärt
Ein Schaltschrank ist eine wichtige Komponente der industriellen Automatisierung und dient als Nervenzentrum für die Steuerung und Überwachung verschiedener elektrischer Geräte. Dieser Artikel befasst sich mit den Grundlagen von Schaltschränken, ihren Komponenten und ihrer Bedeutung für die Gewährleistung eines effizienten und sicheren Betriebs in industriellen Umgebungen.
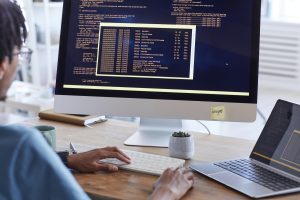
Eine umfassende Anleitung zum Hochladen von Programmen auf Weintek HMI: Methoden und bewährte Vorgehensweisen
Ein umfassender Leitfaden zum Hochladen von Programmen auf Weintek HMI: Methoden und bewährte Verfahren Im Bereich der industriellen Automatisierung, Mensch-Maschine