PLC összekapcsolhatóság: Adatsilók áthidalása az intelligens gyártásban
Tartalomjegyzék
Ez a bejegyzés a PLC-k közötti interakció alapvető értékét vizsgálja, feltárja a főbb interakciós megközelítéseket, értékeli az alapvető protokollokat és azok hatékonyságbeli különbségeit, valamint adatösszehasonlításon és funkcionális kutatáson keresztül útmutatást ad az olvasóknak az ideális interakciós megoldások kiválasztásához és konfigurálásához.
Bevezetés: A PLC összekapcsolhatóság elkerülhetetlensége az intelligens gyártás korszakában
A jelenlegi nemzetközi ipari változások környezetében az ipari automatizálás már nem csupán a termelési hatékonyság növelésére szolgáló eszköz; hanem az adaptálható gyártórendszerek kiépítésének és az adatvezérelt döntéshozatalnak az alapvető pillére.
Az ipari vezérlőrendszerek „agyaként” a programozható logikai vezérlő (PLC) kulcsfontosságú helyet foglal el. Mindazonáltal a bővülő termelési tartományokkal, a folyamatok bonyolultabbá válásával és a dolgok internetének (IoT) technológiáinak mélyreható elsajátításával az önálló PLC-rendszerek gyakran meghibásodnak.
Azonnal szükség van hatékony, stabil és megbízható interakciós kapcsolatok létrehozására a különböző gyártósorokon szétszórt és egyedi feladatokért felelős PLC-k között, hogy zökkenőmentes információmegosztást, integrált berendezések üzemeltetését és a termelési folyamatok nemzetközi optimalizálását lehessen elérni.
A tipikus „info siló” modell valójában jelentős forgalmi dugóvá vált, amely akadályozza az intelligens gyártás fejlődését.
Például, ha egy termékcsomagoló sor PLC-je nem tud valós idejű gyártási információkat lekérni a folyamat felsőbb szakaszán lévő rakodósorról, az ritmusegyenlőtlenségekhez vezet. Hasonlóképpen, ha egy robotvezérlő PLC nem tudja megosztani a hibainformációkat a fő gyártósor PLC-jével, az meghosszabbítja az állásidőt.
Ezek az aggodalmak hangsúlyozzák a PLC-k közötti kommunikáció fontosságát. Ez nemcsak hidat képez az információcsere terén a berendezések szintjén, hanem alapvető alapot teremt a gyári és vállalati szintű adatkombinációhoz, -értékeléshez és -döntéshozatalhoz is.
PLC összekapcsolhatóság: Az intelligens gyártás sarokköve és alapvető értéke
A PLC-k közötti interakció messze túlmutat az egyszerű információátvitelen, ez a modern ipari automatizálási rendszerek kulcsa a következő alapvető értékek elérésében:
Információmegosztás és átláthatóság: A különböző PLC-k között cserélt valós idejű gyártási információk (például eredmény, szerszámok állapota, hibakódok stb.) részletes gyári működési áttekintéssel biztosítják a termelésfelügyeletet. Ez képezi a nagyméretű információelemzés és a karbantartás előrejelzésének információs alapját, segítve a váratlan állásidő csökkentését és a berendezések általános hatékonyságának (OEE) növelését.
Együttműködésen alapuló működés és folyamatoptimalizálás: Az interakció révén több PLC képes együttműködve bonyolult gyártási feladatokat végrehajtani. Például egy automatizált összeszerelő soron a termékadagolást, -kezelést, -ellenőrzést és -csomagolást különböző PLC-k szabályozhatják. Az adatszinkronizáció közöttük garantálja a zökkenőmentes és hatékony gyártási folyamatot.
Központosított menedzsment és távvezérlés: A PLC-k közötti kommunikáció lehetővé teszi a fő vezérlőtermek vagy menedzsment rendszerek (például SCADA, MES) számára, hogy központilag ellenőrizzék, módosítsák a paramétereket, és távolról érzékeljék több PLC-t. Ez jelentősen javítja a rendszer karbantarthatóságát és skálázhatóságát, miközben minimalizálja a funkcionális és karbantartási költségeket.
Alkalmazkodóképes gyártás és gyors reagálás: A gyorsan változó piaci igények miatt a modern gyártóüzemeknek rugalmas termelési képességekre van szükségük. A PLC-k összekapcsolhatósága rugalmasabbá teszi a gyártósorok átkonfigurálását és beállítását. A távoli beállítás és a szoftverek letöltése révén az új termelési feladatok gyorsan adaptálhatók. Lényegében a PLC-k összekapcsolhatósága fontos tényező a digitális gyárak fejlesztésében, lehetővé téve az intelligens döntéshozatalt és erősítve a kockázati versenyt.
Az alapvető kommunikációs módszerek alapos elemzése és összehasonlítása
A PLC-k közötti fő kommunikációs technikák a soros kommunikáció, az identitásos interakció és az ipari Ethernet kommunikáció. Jellemzőik ismerete elengedhetetlen az ideális megoldás kiválasztásához.
Soros kommunikáció:
- Jellemzők: Apránként továbbítja az adatokat. Kevesebb jelvezetéket igényel, így nagyobb távolságokhoz alkalmas.
- Előnyök: Egyszerű elektromos bekötés, alacsonyabb ár, viszonylag jobb hangszigetelés.
- Korlátozások: Viszonylag lassabb átviteli sebesség, minimális valós idejű képesség.
- Tipikus protokollok: Modbus RTU/ASCII, PPI, egyedi RS-232/RS-485 protokollok stb.
Párhuzamos kommunikáció:
- Tulajdonságok: Bájtokban vagy szavakban továbbít információt egyidejűleg több adatvonalon.
- Előnyök: Nagy átviteli sebesség, erős valós idejű kapacitás.
- Korlátozások: Bonyolult kábelezés, rövid átviteli távolság, magasabb ár, zavarérzékeny.
- Gyakori alkalmazások: Elsősorban rövid távolságú, nagy sebességű követelményekhez használják, gyakran PLC modulok között vagy egy PLC és nagy sebességű I/O komponensek között, sokkal ritkábban alkalmazzák a PLC-k közötti csatlakoztatás mainstream megközelítéseként.
Ipari Ethernet kommunikáció:
- Tulajdonságok: Standard Ethernet technológián alapul, de ipari környezetben a hatékonyság és a valós idejű hatékonyság maximalizálására optimalizálva. A TCP/IP protokollcsomagot használja, amely különböző hálózati földrajzi helyeket, például csillag-, busz- és gyűrűhálózatokat támogat.
- Előnyök: Nagy sebesség (100 Mbps/Gbps), nagy adatmennyiség-kapacitás, nagy hálózati rugalmasság, több master és service eszköz támogatása, egyszerű integrálhatóság az IT hálózatokkal, és kiváló skálázhatóság.
- Korlátozások: Viszonylag magasabb kezdeti befektetés, bonyolultabb elrendezés.
Értékelési és kiválasztási útmutató a mainstream kommunikációs protokollokhoz
Az interakciós eljárások az információcsere „nyelvét” alkotják, amelyek meghatározzák az információátvitel stílusát, időzítését és hibakezelő eszközeit. A PLC-k közötti interakció során az ideális eljárás kiválasztása központi szerepet játszik a rendszer elrendezésében.
Modbus protokoll
- Bevezetés: A Modbus egy tartós, nyílt és széles körben alkalmazott soros kommunikációs protokoll, amely olyan fizikai felhasználói interfészeket támogat, mint az RS-232 és az RS-485. Fejlődött belőle a Modbus TCP is, amely az Etherneten alapul.
- Jellemzők: Egyszerű eljárás-keretrendszer, könnyen alkalmazható és hibakereshető. Támogatja a master-slave beállítást, ahol egy master több szolgát is kezelhet. Gazdag információtípusok, beleértve a tekercseket és regisztereket.
- Alkalmazások: Gyakran használják különböző PLC márkák közötti, vagy PLC-k és eszközök közötti interakcióhoz, érzékelők, HMI-k, különösen kevésbé szigorú valós idejű igényekkel járó helyzetekben, vagy általános célú interfészként.
PPI protokoll (pont-pont interfész)
- Áttekintés: A PPI egy soros kommunikációs protokoll, amely kizárólag a Siemens S7-200 sorozatú PLC-kben található, és az RS-485 fizikai rétegen alapul.
- Tulajdonságok: Kifejezetten a Siemens S7-200 sorozatú PLC-khez, főként program szoftveralkalmazással (Step7-Micro/Win) történő programfeltöltésre/letöltésre, valamint az S7-200 és a HMI-k közötti kommunikációra használják. Támogatja a master-slave beállítást.
- Alkalmazások: A Siemens S7-200 sorozatú PLC-kre korlátozódik. A jelenlegi mainstream S7-1200/1500 sorozatban nagyrészt felváltotta a PROFINET/Ethernet interakció.
PROFINET protokoll
- Összefoglalás: A PROFINET egy ipari automatizálási kommunikációs eljárás, amelyet a PROFIBUS & PROFINET International (PI) fejlesztett ki, és amely az Ethernet alapokon nyugszik.
- Jellemzők: Nagy sebességű, erős valós idejű képesség (IR_T és számos más valós idejű csatorna támogatása), rugalmas hálózati topológiákat támogat (vonal, csillag, gyűrű), integrálja az elemzési teljesítményt, és elősegíti az egyszerű eszközkezelést és tervezési elrendezést.
- Alkalmazások: Számos PLC márkanév, például a Siemens és a Beckhoff széles körben alkalmazza. Ez a kedvelt választás komplex, nagy sebességű és valós idejű kritikus gyártósorokhoz (pl. autógyártás, csomagológépek).
EtherNet/IP protokoll
- Áttekintés: Az EtherNet/IP (Ethernet Industrial Protocol) egy ipari protokoll, amelyet az ODVA (Open DeviceNet Vendors Association) fejlesztett ki, szintén a szabványos Etherneten alapulva.
- Jellemzők: A Common Industrial Protocol (CIP) szabványt használja a vezérlési, biztonsági, konfigurációs és diagnosztikai funkciók egységesítésére. Támogatja mind az explicit, mind az implicit üzenetküldést a rugalmas adatcsere és a nagy teljesítményű valós idejű vezérlés érdekében.
- Alkalmazások: Széles körben használják a Rockwell Automation termékeivel Allen-Bradley PLC-k és számos más CIP-kompatibilis eszköz. Domináns az észak-amerikai piacon.
Erősítse meg projektjeit vadonatúj, eredeti Omron, Mitsubishi, Schneider PLC segítségével – raktáron, készen áll!
Következtetés
A PLC-k közötti kommunikáció a modern ipari automatizálási rendszerek éltető eleme. Ez a cikk alaposan ismertette központi szerepét az intelligens gyártásban, elmélyedve a soros kommunikáció, a párhuzamos kommunikáció és az ipari Ethernet jellemzőiben és alkalmazási lehetőségeiben.
Összehasonlító táblázatokon keresztül kiemelte a Modbus, PPI, PROFINET és EtherNet/IP protokollok közötti teljesítménybeli különbségeket. Részletes PLC kommunikációs konfigurációs lépéseket és gyakorlati ajánlásokat is ismertettünk, hangsúlyozva minden szakasz fontosságát a megoldástervezéstől a biztonsági védelemig.
Ezen kommunikációs technológiák elsajátítása és rugalmas alkalmazása nemcsak az ipari terepi mérnökök számára elengedhetetlen készség, hanem a vállalatok számára is kulcsfontosságú ahhoz, hogy megőrizzék vezető szerepüket és fenntartható fejlődést érjenek el egy rendkívül versenyképes piacon. Az adatsilók áthidalásával és az összekapcsolhatóság alkalmazásával egy intelligensebb és hatékonyabb ipari korszakba lépünk.
Lépjen kapcsolatba velünk
Csak töltse ki nevét, e-mail címét és kérésének rövid leírását ezen az űrlapon. 24 órán belül felvesszük Önnel a kapcsolatot.
Ezeket a témákat is érdekesnek találhatja
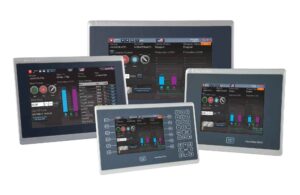
Allen-Bradley PanelView kiválasztási útmutató: Válassza ki a megfelelő HMI-t
Ipari automatizálási igényeinek megfelelő Allen-Bradley PanelView-t keres? Ez az átfogó kiválasztási útmutató végigvezeti Önt mindenen, amit a PanelView Plus 7-ről, a PanelView 800-ról és az Allen-Bradley család többi grafikus termináljáról tudnia kell. Akár meglévő rendszerét frissíti, akár frissen kezdi, ez az útmutató segít megalapozott döntés meghozatalában.
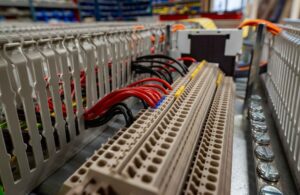
24VDC vs 120VAC: Az automatizálás különbségeinek megértése
Az ipari automatizálás vezérlőfeszültségének kiválasztásakor két gyakori választás a 24 VDC és a 120 VAC. De hogyan dönti el, melyik a megfelelő az Ön alkalmazásához? Ebben a cikkben lebontjuk a 24VDC és 120VAC közötti főbb különbségeket, feltárjuk azok automatizálási rendszerekben való felhasználását, és segítünk az Ön igényei alapján megalapozott döntés meghozatalában.
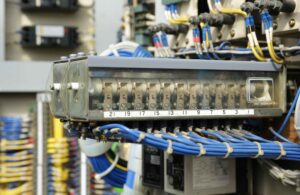
Az Omron PLC-k 10 legfontosabb jellemzője, amelyek iparágvezetővé teszik őket
A programozható logikai vezérlők (PLC) képezik a modern ipari automatizálás gerincét, és az Omron folyamatosan az élen jár e technológia területén. Az Omron PLC-k megbízhatóságukról, sokoldalúságukról és fejlett funkcióikról híresek, így világszerte a legjobb választás az iparágak számára. Ebben a cikkben megvizsgáljuk az Omron PLC-k 10 legfontosabb funkcióját, amelyek megkülönböztetik őket iparági vezetőként.