24VDC vs 120VAC: Az automatizálás különbségeinek megértése
Legyen Ön mérnök, technikus vagy beszerzési menedzser, ez az útmutató tele van hasznos információkkal, amelyek segítenek eligazodni ebben a fontos döntésben.
Tartalomjegyzék
Mi az a 24 VDC és miért használják az automatizálásban?
A 24 VDC-t széles körben használják az automatizálásban, mivel alkalmas alacsony fogyasztású eszközökhöz, beleértve az érzékelőket, reléket és PLC-k. A 24 VDC vezérlőáramkörök általában biztonságosabbak, mint a 120 VAC, mivel az alacsonyabb feszültség csökkenti az áramütés kockázatát. A központokban és az ipari rendszerekben a 24 VDC-t gyakran használják mágnesszelepekben, érzékelőkés a vezérlő vezetékek.
Ez az alacsony feszültségű teljesítmény biztosítja, hogy az áramkörök biztonságosak és megbízhatóak maradjanak, és minimálisra csökkenti az elektromos tüzek kockázatát. A precíz vezérlést igénylő automatizálási alkalmazásoknál a 24 VDC a stabilabb teljesítmény és az alacsonyabb áramerősség előnyét kínálja, ami döntő fontosságú az érzékeny berendezéseknél.
Főbb előnyök:
- Biztonság: Az alacsonyabb feszültség kisebb áramütés vagy sérülés kockázatát jelenti.
- Megbízhatóság: A 24 VDC rendszerek kevésbé érzékenyek a feszültségesésre vagy az interferenciára.
- Hatékonyság: Az alacsonyabb áramigény csökkenti az energiafogyasztást, így ideális a folyamatos működéshez.
Mik a 120 VAC előnyei a vezérlőrendszereknél?
Míg a 120 VAC-ot gyakran használják nagyobb berendezésekben, az ipari vezérlőrendszerekben is gyakori. A 120 VAC azonban elsősorban nagy teljesítményű terhelésekhez és gépekhez használatos. A vezérlőáramkörök általában sok ipari rendszerben 24 VDC tápfeszültséggel rendelkeznek a biztonság javítása, a feszültségesések csökkentése és a megbízható működés biztosítása érdekében.
Az egyik fő oka annak, hogy a 120 VAC-ot széles körben használják a vezérlőrendszerekben, az a rendelkezésre állás és az a képesség, hogy nagy távolságra továbbítsa az energiát. Mivel a magasabb feszültségek kisebb áramot igényelnek ugyanannyi teljesítmény átviteléhez, a 120 VAC rendszerek bizonyos alkalmazásoknál hatékonyabbak lehetnek.
Főbb előnyök:
- Magasabb Erő: Alkalmas nagyobb rendszerekhez, berendezésekhez vagy gépekhez, amelyek több energiát igényelnek.
- Hosszabb távolságok: A 120 VAC hosszabb vezetékeken továbbítható jelentős feszültségesés nélkül.
- Költséghatékony: Könnyebb megvalósítani azokon a területeken, ahol 120 VAC könnyen elérhető.
Miben különbözik a 24VDC vezérlés a 120VAC vezérléstől?
A vezérlőáramkörökben a 24 VDC és a 120 VAC közötti összehasonlítás során a legfontosabb különbségek a biztonságban, a vezetékek bonyolultságában és a támogatott berendezések típusában rejlenek. Például a 24 VDC vezérlőáramkörök gyakran egyszerűbbek és kevesebb védelmet igényelnek, míg a 120 VAC vezérlőáramkörökhöz további alkatrészekre, például megszakítókra, biztosítékokra és robusztusabb vezetékrendszerekre lehet szükség.
A 24 VDC rendszerek általában megbízhatóbbak a kisebb vezérlési alkalmazásokhoz, és széles körben használják PLC-kben és kis teljesítményű érzékelőkben. Másrészt a 120 VAC vezérlőrendszerek megfelelőbbek olyan alkalmazásokhoz, ahol nagyobb teljesítményre van szükség, mint pl motorok és nagy ipari berendezések.
24VDC vezérlés:
- Egyszerűsített vezetékezés.
- Ideális kisebb, kis fogyasztású készülékekhez.
- Megnövelt biztonság a nagyfeszültségű expozíció minimális kockázatával.
120 VAC vezérlés:
- Gyakran használják nagy teljesítményű gépekhez.
- További védelmet és biztonsági intézkedéseket igényel.
- Támogatja a nagyobb, energiaigényesebb eszközöket.
24VDC vs 120VAC: Milyen feszültséget használjon?
A 24 VDC és a 120 VAC összehasonlítása nagymértékben függ az energiaszükséglettől és az alkalmazástól. Kisebb automatizálási berendezések és vezérlőáramkörök esetében általában a 24 VDC a jobb választás. Azonban a 120 VAC a megfelelőbb választás nagyobb gépekhez és nagy távolságokra történő erőátvitelhez, mivel képes nagyobb áramerősséget szállítani kisebb energiaveszteség mellett.
Ezzel szemben a 120 VAC jobban megfelel nagy teljesítményű gépekhez, motorokhoz vagy berendezésekhez, ahol nagyobb feszültség szükséges az optimális teljesítményhez. A használni kívánt feszültség kiválasztásakor vegye figyelembe a következő tényezőket:
Figyelembe veendő tényezők:
- Teljesítménykövetelmények: Ha rendszerének több áramra van szüksége, a 120 VAC lehet a jobb választás.
- Biztonság: A gyakori karbantartást igénylő vagy kezelőket bevonó rendszerek esetében a 24 VDC biztonságosabb lehetőséget kínál.
- Távolság: Hosszú távú vezetékezésnél a 120 VAC hatékonyabb, mivel csökkenti az áramerősséget és minimalizálja a feszültségesést.
Hogyan lehet elhárítani a feszültséggel kapcsolatos problémákat az automatizálási rendszerekben?
Amikor problémák merülnek fel az automatizálási rendszerekben, gyakran a feszültséggel kapcsolatos problémák hibaelhárítása az első lépés. Az olyan problémák, mint a feszültségesés, a nem megfelelő feszültségellátás vagy a berendezés meghibásodása, jelentős fennakadásokat okozhatnak az ipari automatizálásban.
Gyakori feszültségproblémák:
- Feszültségesés: Nagy távolságokon a feszültség leeshet, ami nem hatékony energiaellátáshoz vezethet. A 24 VDC rendszerekben ez különösen észrevehető a vezérlőáramkörökben, amelyek még kis feszültségesésre is érzékenyek.
- Helytelen feszültség: Győződjön meg arról, hogy az adott alkalmazáshoz a megfelelő 24 VDC vezérlést vagy 120 VAC tápegységet használja. Nem megfelelő feszültség használata károsíthatja az érzékeny alkatrészeket.
- Berendezés meghibásodások: A transzformátorokkal, relékkel vagy PLC-kkel kapcsolatos problémák adódhatnak a feszültség inkonzisztenciái miatt.
Hibaelhárítási tippek:
- Ellenőrizze a tápegységet: Győződjön meg arról, hogy az áramforrás megfelelő feszültséget biztosít a rendszer számára.
- Vizsgálja meg a vezetékeket: Vizsgálja meg a vezérlőkábeleket sérülés, korrózió vagy nem megfelelő csatlakozások szempontjából.
- Mérje meg a feszültséget: Multiméterrel mérje meg a tényleges feszültséget a rendszer bemeneti és kimeneti pontjain, hogy az a várt tartományon belül legyen.
Gyakran Ismételt Kérdések
Mi a különbség a 24VDC és a 120VAC között az ipari automatizálásban?
A 24 VDC-t alacsony fogyasztású alkalmazásokhoz, például PLC-khez és érzékelőkhöz használják, biztonságot és energiahatékonyságot kínálva, míg a 120 VAC nagyobb teljesítményű alkalmazásokhoz, például motorokhoz és nagyobb gépekhez.
A 24 VDC biztonságosabb, mint a 120 VAC?
Igen, a 24 VDC biztonságosabbnak tekinthető, mivel kisebb áramütési kockázatot jelent, mint a magasabb 120 VAC feszültség.
Használhatok 120 VAC vezérlőáramköröket 24 VDC helyett?
Míg a 120 VAC használható vezérlőáramkörökhöz, általában nagy teljesítményű alkalmazásokhoz van fenntartva. Biztonsága és megbízhatósága miatt a 24VDC jobban megfelel az automatizálás vezérlőáramköreinek.
Hogyan háríthatom el a feszültségesést egy 24 VDC rendszerben?
Mérje meg a feszültséget a rendszer különböző pontjain, és ellenőrizze, hogy nincsenek-e laza csatlakozások vagy sérült vezetékek. A feszültségesés nagy távolságok esetén a leginkább észrevehető, ezért ügyeljen arra, hogy a vezetékezés megfelelő legyen a távolságnak.
Melyik az energiatakarékosabb, 24VDC vagy 120VAC?
A 24 VDC jellemzően energiahatékonyabb a kisebb rendszerekben, mivel kisebb áramot igényel, és ideális kis teljesítményű eszközökhöz. A 120 VAC hatékonyabb a nagy távolságok átviteléhez.
Erősítse meg projektjeit vadonatúj, eredeti Omron, Mitsubishi, Schneider PLC segítségével – raktáron, készen áll!
Következtetés
- 24VDC ideális kis teljesítményű alkalmazásokhoz, biztonságot és energiahatékonyságot biztosítva a vezérlőáramkörökben.
- 120VAC alkalmasabb nagy teljesítményű gépekhez és berendezésekhez, különösen ahol nagy távolságra van szükség erőátvitelre.
- A 24 VDC és 120 VAC közötti választás az automatizálási rendszer teljesítményigényétől, biztonsági szempontjaitól és hatékonyságától függ.
- Mindig győződjön meg arról, hogy a megfelelő feszültséget használja a berendezéshez, hogy elkerülje a károsodást vagy a hatástalanságot.
Ezeket a tényezőket figyelembe véve megalapozottabb döntést hozhat, amely biztosítja ipari automatizálási rendszereinek megbízhatóságát, biztonságát és hatékonyságát.
Új, eredeti PLC-ket keres projektjeihez? A Kwoco-nál a legfrissebb PLC-ket kínáljuk olyan legnépszerűbb márkáktól, mint például Omron, Mitsubishi, és Schneider. Vásároljon bizalommal – gyors szállítás, garantált minőség! Vásároljon most
Lépjen kapcsolatba velünk
Csak töltse ki nevét, e-mail címét és kérésének rövid leírását ezen az űrlapon. 24 órán belül felvesszük Önnel a kapcsolatot.
Ezeket a témákat is érdekesnek találhatja
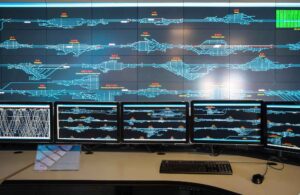
PLC összekapcsolhatóság: Adatsilók áthidalása az intelligens gyártásban
Az Ipar 4.0 egyre növekvő áramlatában az ipari automatizálási rendszerek jelentősen bonyolultabbá válnak, és az önálló PLC-k már nem elegendőek a fejlődő gyártási igények kielégítésére.
A PLC-k közötti megbízható és hiteles összekapcsolhatóság létfontosságúvá vált az információs silók felszámolása és az intelligens termelés lehetővé tétele érdekében.
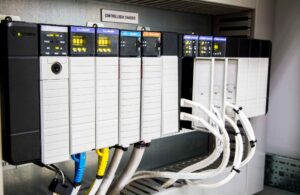
Allen-Bradley vs ABB: Melyik a legjobb az ipari automatizáláshoz?
Az ipari automatizálás gyorsan fejlődő világában gyakran két név tűnik fel: Allen-Bradley és ABB. Mindketten óriások az iparágban, és olyan élvonalbeli megoldásokat kínálnak, mint a PLC-k, VFD-k és vezérlők. De vajon ugyanazok? Ez a cikk e két márka finomságait kutatja, összehasonlítja kínálatukat, hogy segítsen megalapozott döntéseket hozni a vezérlőrendszerekkel kapcsolatban.
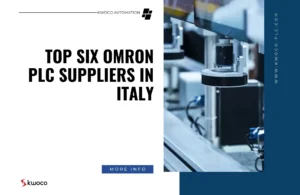
A hat legnépszerűbb Omron PLC beszállító Olaszországban
A hat legjobb Omron PLC beszállító Olaszországban Mint valaki, aki mélyen érintett az ipari automatizálási szektorban, különösen a nemzetközi kereskedelemben