Qu'est-ce que DCS ? Guide des systèmes de contrôle distribués
Table des matières
Comprendre les systèmes de contrôle distribués (DCS)
Un système de contrôle distribué (DCS) est un système de contrôle automatisé qui surveille et contrôle les processus industriels en décentralisant les fonctions de contrôle dans l'ensemble du système. Contrairement aux systèmes de contrôle centralisés traditionnels, un DCS répartit les éléments de contrôle sur différents emplacements d'une usine ou d'une zone de traitement.
Qu'est-ce qui constitue un DCS ?
Les composants d'un DCS comprennent :
- Unités de contrôle:Responsable de l'exécution des algorithmes de contrôle et de la gestion des boucles de contrôle.
- Interface homme-machine (IHM):Permet aux opérateurs de surveiller et de contrôler les processus.
- Réseaux de communication:Facilite l'échange de données entre les systèmes.
- Systèmes d'acquisition de données:Collecte et traite les données provenant de capteurs et d'instruments.
Ces composants fonctionnent ensemble pour fournir une surveillance et un contrôle en temps réel, garantissant un contrôle efficace des processus industriels.
Architecture DCS : comment ça marche ?
L'architecture d'un système de contrôle distribué est conçue pour répartir les tâches de contrôle sur plusieurs contrôleurs et réseaux. Cette architecture distribuée améliore la fiabilité et les performances du système en éliminant les points de défaillance uniques.
Principales caractéristiques de l'architecture DCS
- Fonctions de contrôle distribuées:Les éléments de contrôle sont répartis dans tout le système, permettant une surveillance et un contrôle en temps réel.
- Systèmes intégrés:DCS peut être intégré à d'autres systèmes tels que SCADA et PLC pour un contrôle complet.
- Redondance:Fournit des systèmes de sauvegarde pour assurer un fonctionnement continu même en cas de défaillance d'un composant.
Applications du DCS dans les procédés industriels
Les systèmes DCS sont largement utilisés dans les industries qui nécessitent un contrôle et une surveillance précis des processus, tels que :
- Usines chimiques et pétrochimiques
- Installations de production d'énergie
- Industries pétrolières et gazières
- Fabrication pharmaceutique
Pourquoi utiliser DCS dans ces industries ?
- Contrôle efficace:DCS permet un contrôle efficace des systèmes de production.
- Surveillance en temps réel:Les opérateurs peuvent surveiller et contrôler les processus en temps réel.
- Sécurité:Améliore la sécurité des opérations grâce au contrôle et à la surveillance automatisés.
- Évolutivité:Facilement évolutif pour s'adapter aux processus industriels en expansion.
En répartissant les tâches de contrôle, DCS permet aux opérateurs de surveiller et de contrôler efficacement les processus industriels complexes.
Avantages de la mise en œuvre d'un DCS
La mise en œuvre d’un système de contrôle distribué offre de nombreux avantages :
Fiabilité et performances améliorées
- Redondance:Réduit le risque de défaillances du système.
- Contrôle distribué:Minimise l’impact des problèmes localisés sur l’ensemble du système.
Contrôle et surveillance améliorés
- Données en temps réel:Fournit aux opérateurs des données en temps réel à l'aide d'algorithmes de contrôle.
- Stratégies de contrôle avancées:Prend en charge des méthodes de contrôle avancées pour des processus optimisés.
Intégration avec d'autres systèmes
- Intégration transparente:DCS peut être intégré aux PLC, aux systèmes SCADA et aux systèmes de gestion.
- Partage de données:Facilite l’échange de données entre les systèmes pour une meilleure prise de décision.
DCS vs PLC : quelle est la différence ?
Bien que les DCS et les PLC (contrôleurs logiques programmables) soient tous deux utilisés dans les applications d'automatisation et de contrôle industrielles, ils servent à des fins différentes.
Système de contrôle distribué (DCS)
- Processus complexes:Idéal pour les processus continus et complexes nécessitant un contrôle précis.
- Architecture distribuée:Les fonctions de contrôle sont réparties dans tout le système.
- Contrôle et surveillance intégrés:Combine le contrôle et la surveillance dans un seul système
Automate programmable industriel (API)
- Contrôle discret:Idéal pour les applications de contrôle discrètes telles que les chaînes de montage.
- Contrôle centralisé:Utilise généralement un système de contrôle centralisé.
- Évolutivité:Plus facile à mettre à l'échelle pour les petites applications.
Questions fréquemment posées
Un DCS est utilisé pour contrôler les processus industriels qui nécessitent un contrôle précis et fiable, comme dans les usines chimiques, les centrales électriques et les raffineries de pétrole. Il répartit les fonctions de contrôle sur l'ensemble du système pour un contrôle et une surveillance efficaces.
Bien que les deux soient utilisés pour le contrôle et la surveillance, un DCS est conçu pour des processus complexes et continus avec des fonctions de contrôle intégrées, tandis que les systèmes SCADA sont utilisés pour la surveillance et le contrôle à distance sur de vastes zones géographiques.
Oui, un DCS peut être intégré à d’autres systèmes tels que des PLC, des SCADA et des systèmes de gestion pour fournir une vue complète de l’ensemble du processus et améliorer les stratégies de contrôle.
Les principaux composants d'un DCS comprennent les unités de contrôle, les interfaces homme-machine (IHM), les réseaux de communication et les systèmes d'acquisition de données.
Le DCS est essentiel car il fournit un contrôle précis, une surveillance en temps réel et une fiabilité améliorée du système, qui sont essentiels pour des applications d'automatisation et de contrôle industrielles efficaces et sûres.
Alimentez vos projets avec des PLC Omron, Mitsubishi, Schneider flambant neufs et originaux – en stock, prêts maintenant !
Conclusion
En résumé, un système de contrôle distribué (DCS) est un composant essentiel de l'automatisation et du contrôle industriels modernes. Il permet la surveillance et le contrôle en temps réel de processus industriels complexes en répartissant les tâches de contrôle dans l'ensemble du système. En s'intégrant à d'autres systèmes et en fournissant des stratégies de contrôle avancées, le DCS améliore l'efficacité, la fiabilité et la sécurité dans diverses applications industrielles.
- Définition du DCS:Un système de contrôle automatisé avec des fonctions de contrôle distribuées.
- Architecture:Conçu pour distribuer les éléments de contrôle pour une fiabilité accrue.
- Applications:Utilisé dans les industries nécessitant un contrôle précis des processus continus.
- Avantages: Améliore l’efficacité, la fiabilité et l’intégration avec d’autres systèmes de contrôle.
- DCS contre PLC:DCS est destiné aux processus complexes ; PLC est destiné aux applications de contrôle discret.
Pour plus d'informations sur les produits d'automatisation associés, consultez nos pages sur PLC, Mitsubishi, et Schneider PLC.
Contactez-nous
Remplissez simplement votre nom, votre adresse e-mail et une brève description de votre demande dans ce formulaire. Nous vous contacterons dans les 24 heures.
Catégorie de produit
Produits en vente à chaud
Ces sujets pourraient également vous intéresser
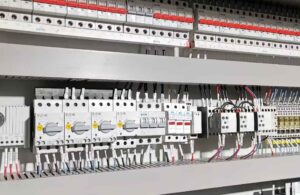
Capteur de proximité vs capteur photoélectrique
Cet article aborde le domaine fascinant des capteurs de proximité et des capteurs photoélectriques, en explorant leurs fonctionnalités, leurs différences et leurs applications. Que vous soyez un ingénieur chevronné dans une usine de machines et d'équipements ou un fournisseur de solutions à la recherche des meilleurs composants d'automatisation, il est essentiel de comprendre ces types de capteurs. En tant qu'usine de fabrication de produits d'automatisation et de contrôle industriels, nous sommes là pour éclairer les subtilités de ces composants essentiels, vous guidant finalement vers des décisions éclairées pour vos projets.
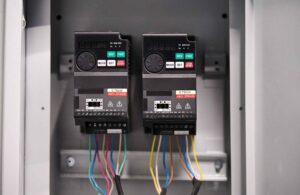
Comprendre le VFD : qu'est-ce qu'un variateur de fréquence ?
Dans le domaine de l'automatisation industrielle, les variateurs de fréquence (VFD) sont des composants essentiels qui améliorent l'efficacité et les performances des systèmes de moteurs électriques. Cet article explore les principes fondamentaux des VFD, leurs fonctionnalités et les nombreux avantages qu'ils offrent en termes de contrôle de la vitesse et d'efficacité énergétique.
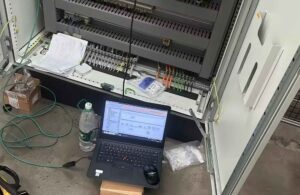
Programmation PLC : un guide complet pour les débutants
Dans le monde actuel, où l'automatisation industrielle et la production intelligente révolutionnent le monde, l'automate programmable industriel (API) est devenu le cœur de tout système automatisé. Pour les particuliers et les entreprises souhaitant se lancer ou progresser dans le secteur de l'automatisation, la maîtrise des programmes API n'est pas seulement une compétence, c'est la clé de l'avenir.