Menyelesaikan Masalah Kegagalan PLC Biasa: Panduan untuk Pengawal Logik Boleh Aturcara
Panduan ini menyelidiki punca biasa PLC kegagalan dan menyediakan petua penyelesaian masalah praktikal untuk membantu anda mengekalkan prestasi optimum dalam sistem PLC anda.
Jadual Kandungan
Apakah Menyebabkan Kegagalan PLC dalam Sistem Kawalan?
Memahami sebab di sebalik kegagalan PLC adalah penting untuk mengekalkan sistem kawalan yang cekap. Berikut adalah beberapa isu biasa yang boleh membawa kepada masalah PLC.
Haus dan Koyak Komponen Dalaman
Dari masa ke masa, komponen dalaman dalam PLC, seperti unit pemprosesan pusat (CPU) dan modul, mungkin mengalami haus dan lusuh akibat operasi berterusan.
- Isu CPU: Masalah dengan CPU boleh menyebabkan ketidakstabilan atau kegagalan sistem.
- Modul rosak: Modul PLC, termasuk modul input/output, boleh gagal, menyebabkan gangguan sistem.
- Rasuah Memori PLC: Memori PLC menyimpan program dan data; rasuah boleh menyebabkan tingkah laku yang tidak dapat diramalkan.
Faktor Luaran dan Keadaan Persekitaran
Faktor luaran boleh memberi kesan ketara kepada prestasi PLC.
- Bunyi Elektrik dan Gangguan Elektromagnet (EMI): Bunyi elektrik dan EMI boleh mengganggu isyarat dalam sistem PLC.
- Voltan turun naik: Isu voltan boleh menyebabkan masalah bekalan kuasa, menjejaskan operasi PLC.
- Persekitaran Perindustrian Yang Keras: Pendedahan kepada suhu dan habuk yang melampau boleh merosakkan komponen dalaman.
Kesilapan Manusia dan Amalan Penyelenggaraan
Kesilapan manusia dan penyelenggaraan yang lemah boleh menyebabkan kegagalan PLC.
- Pengaturcaraan yang salah: Ralat dalam program PLC boleh menyebabkan sistem tidak berfungsi.
- Penyelenggaraan Tidak Betul: Mengabaikan pembaikan dan penyelenggaraan boleh mengakibatkan haus dan lusuh tanpa disedari.
- Sambungan Longgar: Sambungan longgar dalam modul kawalan PLC atau dengan peranti medan boleh menyebabkan isu terputus-putus.
Dengan mengetahui punca biasa kegagalan PLC ini, anda boleh melaksanakan strategi untuk mengelakkan masalah ini dan memastikan sistem PLC anda kekal andal.
Bagaimanakah Gangguan Bunyi Elektrik Mempengaruhi Prestasi PLC?
Gangguan bunyi elektrik ialah isu penting yang boleh menyebabkan kerosakan PLC dan ketidakstabilan sistem.
Memahami Bunyi Elektrik
Bunyi elektrik merujuk kepada gangguan yang tidak diingini yang menjejaskan litar elektrik.
- Gangguan Elektromagnet (EMI): Disebabkan oleh peranti seperti motor, yang membawa kepada gangguan dalam PLC.
- Gangguan Frekuensi Radio (RFI): Dipancarkan oleh peranti wayarles dan boleh menjejaskan komunikasi PLC.
Kesan ke atas Sistem PLC
- Kehilangan Data: Bunyi elektrik boleh merosakkan data dalam PLC.
- Ranap Sistem: Gangguan yang teruk boleh menyebabkan sistem PLC ditetapkan semula atau ranap.
- Kegagalan Bersekala: Membawa kepada masalah PLC yang tidak dapat diramalkan yang sukar untuk didiagnosis.
Strategi Mitigasi
- Pembumian yang betul: Memastikan integriti tanah dengan wayar pembumian khusus mengurangkan gangguan.
- Kabel Terlindung: Penggunaan kabel berperisai untuk meminimumkan gangguan bunyi elektrik.
- Penapis EMI/RFI: Memasang penapis untuk menyekat isyarat yang tidak diingini.
Melaksanakan strategi ini membantu menghalang bunyi elektrik daripada mengganggu sistem PLC anda.
Menyelesaikan Masalah Kegagalan Modul dalam Sistem PLC
Kegagalan modul adalah isu biasa yang boleh menyebabkan kegagalan sistem dalam sistem kawalan PLC.
Mengenalpasti Kegagalan Modul
- Kod Ralat dan Mesej Kesalahan: PLC mungkin memaparkan kod tertentu yang menunjukkan isu.
- Bacaan Tidak Konsisten: Peranti medan mungkin memberikan data yang tidak menentu.
- Ketidakstabilan Sistem: Sistem mungkin menjadi tidak stabil atau mengalami ranap sistem.
Punca Biasa
- Isu Voltan: Voltan lebih atau kurang boleh merosakkan modul.
- Pakai dan Koyak: Penggunaan yang berpanjangan boleh menyebabkan kehausan modul.
- Sambungan Longgar: Sambungan ke modul atau peranti medan mungkin menjadi longgar.
Langkah Penyelesaian Masalah
- Semak Tahap Voltan: Pastikan bekalan kuasa memberikan voltan yang betul.
- Periksa Sambungan: Ketatkan sebarang sambungan yang longgar.
- Gantikan Modul yang Bermasalah: Tukar modul yang menunjukkan tanda-tanda kegagalan.
Dengan menangani kegagalan modul dengan segera, anda boleh mengekalkan kebolehpercayaan sistem kawalan PLC anda.
Kepentingan Integriti Tanah dalam Operasi PLC
Integriti tanah adalah penting untuk operasi PLC yang selamat dan cekap.
Faedah Pembumian yang Betul
- Mengurangkan Bunyi Elektrik: Meminimumkan EMI dan RFI, memastikan integriti isyarat.
- Menghalang Gelung Tanah: Mengelak laluan semasa yang tidak diingini yang boleh mengganggu PLC.
- Meningkatkan Keselamatan: Melindungi daripada kejutan elektrik dan kerosakan peralatan.
Isu Asas Biasa
- Pemasangan Tidak Betul: Pembumian yang salah boleh menimbulkan lebih banyak bunyi.
- Kakisan dan Kerosakan: Boleh menjejaskan wayar pembumian, menjejaskan integriti tanah.
Amalan Terbaik
- Pemeriksaan Berkala: Periksa sistem pembumian untuk tanda-tanda haus dan lusuh.
- Gunakan Kawasan Khusus: Mencegah gangguan daripada peralatan lain.
- Ikut Piawaian Industri: Mematuhi garis panduan untuk pembumian dalam persekitaran perindustrian.
Pembumian yang betul memastikan sistem PLC anda beroperasi tanpa gangguan daripada bunyi elektrik.
Menangani Isu Bekalan Kuasa dalam PLC
Isu bekalan kuasa boleh menyebabkan gangguan yang ketara dalam sistem PLC.
Masalah Bekalan Kuasa Biasa
- Lonjakan Kuasa: Boleh merosakkan komponen dalaman PLC.
- Voltan turun naik: Membawa kepada ketidakstabilan dalam sistem PLC.
- Kegagalan Kuasa: Kehilangan sepenuhnya kuasa menghentikan operasi.
Penyelesaian
- Perlindungan Lonjakan: Pasang peranti untuk melindungi daripada lonjakan.
- Bekalan Kuasa Tidak Terputus (UPS): Menyediakan sumber kuasa sandaran untuk PLC.
- Penyelenggaraan Berkala: Periksa bekalan kuasa untuk tanda-tanda kegagalan.
Punca Isu Bekalan Kuasa
- Kegagalan Grid: Isu kuasa luaran yang menjejaskan bekalan kuasa kepada PLC.
- Kegagalan Komponen Dalaman: Kerosakan dalam modul kuasa PLC.
- Faktor Luaran: Keadaan persekitaran yang menyebabkan masalah bekalan kuasa.
Dengan mengurus isu bekalan kuasa secara proaktif, anda boleh mengelakkan kegagalan PLC yang tidak dijangka.
Soalan Lazim
Apakah tanda-tanda biasa kegagalan PLC yang akan berlaku?
Tanda-tanda termasuk kegagalan sekejap-sekejap, ranap sistem yang tidak dijangka, kod ralat dan tingkah laku luar biasa daripada peranti medan.
Bagaimanakah saya boleh meminimumkan bunyi elektrik dalam sistem PLC saya?
Gunakan kabel terlindung, pastikan pembumian yang betul dan pasang penapis EMI/RFI untuk mengurangkan gangguan bunyi elektrik.
Mengapa pembumian penting untuk PLC?
Pembumian yang betul mengurangkan bunyi elektrik, menghalang gelung pembumian dan meningkatkan kestabilan dan keselamatan sistem.
Apakah yang menyebabkan kegagalan modul dalam PLC?
Punca termasuk isu voltan, haus dan lusuh dan sambungan longgar dengan modul atau peranti medan.
Kuasakan projek anda dengan Omron, Mitsubishi, Schneider PLC yang baharu dan asli – dalam stok, sedia sekarang!
Kesimpulan
Dengan memahami dan menangani isu biasa ini, anda boleh memastikan pengawal logik boleh atur cara anda berjalan dengan cekap, memastikan operasi lancar dalam proses automasi anda. Langkah proaktif dan penyelenggaraan tetap adalah kunci untuk mencegah kegagalan PLC dan meminimumkan masa henti.
Mencari PLC baharu yang asli untuk projek anda? Di Kwoco, kami menyimpan PLC terkini daripada jenama terkenal seperti Omron, Mitsubishi, dan Schneider. Beli dengan yakin—penghantaran pantas, kualiti terjamin! Beli Sekarang
Hubungi Kami
Cuma isi nama, alamat e-mel dan penerangan ringkas tentang pertanyaan anda dalam borang ini. Kami akan menghubungi anda dalam masa 24 jam.
Anda Juga Mungkin Mendapatkan Topik Ini Menarik
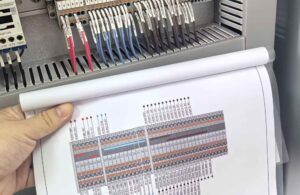
Panduan PLC: Konsep, Aplikasi & Keperluan Pendawaian
Dokumen ini menyediakan analisis komprehensif bagi Pengawal Logik Boleh Aturcara (PLC), meliputi konsep terasnya, keupayaan berkuasa dan metodologi pendawaian asasnya. Kami akan membezakan sistem kawalan berasaskan geganti tradisional dengan sistem berasaskan PLC, menyerlahkan peranan PLC yang amat diperlukan dalam automasi industri moden. Dengan meneroka lima domain aplikasi utama PLC (Kawalan Digital, Kawalan Pergerakan, Kawalan Analog, Pengendalian Data, dan Komunikasi & Rangkaian), dan menganalisis ciri jenis output yang berbeza menggunakan jadual dan data, artikel ini berfungsi sebagai panduan pengenalan terperinci untuk pemula, jurutera dan peminat teknologi.
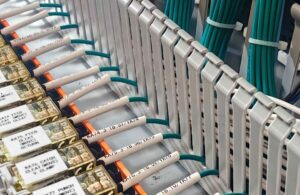
Geganti Elektrik: Memahami Pelbagai Jenis Geganti
Artikel ini menyelidiki dunia geganti yang menarik, meneroka pelbagai jenis, fungsi dan aplikasinya. Sebagai pembekal terkemuka dalam sektor automasi industri, kami memahami peranan penting yang dimainkan oleh geganti dalam mesin dan peralatan kilang, kilang pembuatan dan syarikat penyelesaian kilang. Panduan komprehensif ini bukan sahaja akan meningkatkan pemahaman anda tentang geganti tetapi juga menunjukkan sebab kepakaran kami dalam produk kawalan industri menjadikan kami rakan kongsi yang ideal untuk keperluan automasi anda.
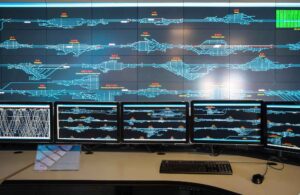
Kesalinghubungan PLC: Merapatkan Silo Data untuk Pembuatan Pintar
Di antara gelombang Industri 4.0 yang melonjak, sistem automasi industri berkembang dengan ketara yang rumit, dan PLC kendiri tidak lagi mencukupi untuk memenuhi keperluan pembuatan yang sedang dibangunkan.
Kesalinghubungan yang boleh dipercayai dan dipercayai antara PLC telah menjadi yang terpenting untuk merosakkan silo maklumat dan membolehkan pengeluaran pintar.