RTD dan Thermocouples: Penderia Penting untuk Automasi Perindustrian
Sama ada anda seorang juruteknik berpengalaman atau baru dalam bidang ini, memahami fungsi, kelebihan dan aplikasi penderia ini akan meningkatkan keupayaan anda untuk melaksanakan penyelesaian pemantauan suhu yang berkesan.
Jadual Kandungan
Apakah RTD dan Bagaimana Ia Berfungsi?
Pengesan Suhu Rintangan (RTD) adalah ketepatan penderia digunakan untuk mengukur suhu dengan mengaitkan rintangan unsur RTD dengan suhu. Biasanya diperbuat daripada platinum tulen, nikel atau tembaga, RTD menawarkan ketepatan dan kestabilan yang tinggi, menjadikannya amat diperlukan dalam pelbagai aplikasi perindustrian.
Bagaimana RTD Mengukur Suhu
RTD beroperasi berdasarkan prinsip bahawa rintangan elektrik logam tertentu boleh diramalkan dengan suhu. Apabila suhu meningkat, rintangan unsur RTD juga meningkat. Perubahan ini diukur dan ditukar kepada bacaan suhu, selalunya melalui a PLC kad input atau sistem pemantauan suhu lain.
Jenis Konfigurasi RTD
RTD datang dalam konfigurasi wayar yang berbeza—2-wayar, 3-wayar dan 4-wayar—setiap satu menawarkan tahap ketepatan dan pampasan yang berbeza-beza untuk rintangan wayar plumbum. RTD 3-wayar biasanya digunakan dalam tetapan industri kerana ia memberikan keseimbangan yang baik antara kerumitan dan ketepatan.
Bagaimanakah RTD Berbanding dengan Termokopel dalam Pengukuran Suhu?
Apabila ia datang kepada penderiaan suhu, RTD dan termokopel ialah dua pesaing utama. Memahami perbezaan mereka adalah kunci untuk memilih penderia yang sesuai untuk aplikasi anda.
Ketepatan dan Kestabilan
RTD terkenal dengan ketepatan unggul dan kestabilan jangka panjang berbanding termokopel. Mereka biasanya menawarkan toleransi ±0.1°C, menjadikannya sesuai untuk aplikasi yang memerlukan kawalan suhu yang tepat.
Julat Suhu
Walaupun RTD sangat baik untuk julat suhu yang luas, termokopel cemerlang dalam mengukur suhu yang sangat tinggi atau rendah, selalunya melebihi julat yang boleh dikendalikan oleh RTD. Sebagai contoh, termokopel Jenis K boleh mengukur suhu sehingga 1,800°C, manakala RTD biasanya terhad kepada sekitar 850°C.
Masa Tindak Balas
Termokopel secara amnya mempunyai masa tindak balas yang lebih cepat kerana pembinaannya yang lebih ringkas, menjadikannya sesuai untuk proses dinamik di mana perubahan suhu yang pantas perlu dikesan dengan pantas.
Apakah Faktor yang Mempengaruhi Toleransi Penderia RTD?
Toleransi penderia RTD merujuk kepada ketepatan dan kebolehpercayaannya dalam mengukur suhu. Beberapa faktor boleh mempengaruhi toleransi RTD, memastikan pemantauan suhu yang tepat.
Kualiti Bahan
Ketulenan unsur RTD, selalunya platinum, memberi kesan ketara kepada toleransinya. Bahan ketulenan tinggi mempamerkan perubahan rintangan yang lebih boleh diramal dengan suhu, meningkatkan ketepatan.
Penentukuran
Penentukuran tetap memastikan penderia RTD mengekalkan ketepatannya dari semasa ke semasa. Penentukuran melibatkan membandingkan bacaan RTD dengan standard suhu yang diketahui dan melaraskan jika perlu.
Keadaan Persekitaran
Faktor seperti bunyi elektrik, getaran dan suhu ambien boleh memberi kesan kepada prestasi RTD. Amalan perisai dan pemasangan yang betul membantu mengurangkan kesan ini, mengekalkan toleransi sensor.
Apakah Peranan yang Dimainkan oleh Wayar dalam Prestasi Penderia RTD?
Pendawaian penderia RTD memainkan peranan penting dalam memastikan pengukuran suhu yang tepat. Bilangan wayar dan kualitinya boleh mempengaruhi prestasi dan kebolehpercayaan sensor.
Konfigurasi Wayar
RTD tersedia dalam konfigurasi 2-wayar, 3-wayar dan 4-wayar:
- 2-Wire RTD adalah yang paling mudah tetapi lebih mudah terdedah kepada ralat disebabkan oleh rintangan wayar plumbum.
- 3-Wire RTD menawarkan pampasan yang lebih baik untuk rintangan wayar plumbum, memberikan ketepatan yang lebih baik.
- 4-Wire RTD memberikan ketepatan tertinggi dengan menghapuskan sepenuhnya rintangan wayar plumbum daripada pengukuran.
Bahan dan Kualiti Wayar
Menggunakan wayar platinum berkualiti tinggi memastikan perubahan rintangan minimum yang tidak berkaitan dengan variasi suhu. Selain itu, pelindung wayar yang betul boleh menghalang bunyi elektrik daripada menjejaskan bacaan penderia.
Amalan Pemasangan
Pemasangan yang betul, termasuk penggunaan telaga terma, boleh melindungi sensor RTD daripada faktor persekitaran dan tekanan mekanikal, memelihara integriti sambungan wayar dan prestasi sensor keseluruhan.
Bagaimanakah PLC Bersepadu dengan Penderia RTD dalam Automasi Perindustrian?
Pengawal Logik Boleh Aturcara (PLC) adalah penting kepada sistem automasi industri moden, dan penyepaduan lancar mereka dengan penderia RTD adalah penting untuk pemantauan dan kawalan suhu yang berkesan.
Menyambung RTD ke PLC
Penderia RTD bersambung ke PLC melalui kad input yang direka untuk mentafsir perubahan rintangan RTD kepada data suhu yang bermakna. Modul input ini selalunya menampilkan keupayaan input analog untuk mengendalikan sifat pengukuran suhu yang berterusan.
Pemprosesan dan Kawalan Data
Setelah disambungkan, PLC memproses data suhu untuk membuat keputusan masa nyata. Contohnya, jika suhu melebihi titik set, PLC boleh mencetuskan tindakan seperti mengaktifkan sistem penyejukan atau melaraskan kelajuan motor untuk mengekalkan keadaan optimum.
Meningkatkan Kebolehpercayaan Sistem
Mengintegrasikan RTD dengan PLC membolehkan strategi pemantauan dan kawalan yang canggih, meningkatkan kebolehpercayaan dan kecekapan keseluruhan proses perindustrian. Selain itu, PLC boleh log data suhu untuk tujuan penentukuran dan penyelenggaraan ramalan, mengurangkan masa henti dan kos operasi.
Soalan Lazim
Apakah kelebihan utama menggunakan RTD berbanding termokopel?
RTD menawarkan ketepatan yang lebih tinggi dan kestabilan jangka panjang yang lebih baik berbanding termokopel, menjadikannya sesuai untuk aplikasi yang memerlukan pengukuran suhu yang tepat.
Bagaimanakah konfigurasi wayar mempengaruhi prestasi RTD?
Konfigurasi wayar (2-wayar, 3-wayar atau 4-wayar) memberi kesan kepada ketepatan bacaan suhu dengan mengimbangi rintangan wayar plumbum. Lebih banyak wayar biasanya memberikan ketepatan yang lebih baik.
Bolehkah RTD mengukur suhu yang sangat tinggi seperti termokopel?
RTD mempunyai julat suhu yang lebih terhad berbanding termokopel. Walaupun ia sesuai untuk kebanyakan aplikasi perindustrian, termokopel lebih disukai untuk mengukur suhu yang sangat tinggi atau rendah.
Berapa kerapkah penderia RTD harus ditentukur?
Penentukuran tetap disyorkan untuk mengekalkan ketepatan, biasanya setiap tahun atau seperti yang ditentukan oleh piawaian pengilang atau industri.
Kuasakan projek anda dengan Omron, Mitsubishi, Schneider PLC yang baharu dan asli – dalam stok, sedia sekarang!
Kesimpulan
- RTD adalah penderia suhu yang sangat tepat dan stabil sesuai untuk aplikasi industri yang tepat.
- Termokopel menawarkan julat suhu yang lebih luas dan masa tindak balas yang lebih cepat tetapi kurang tepat berbanding RTD.
- Konfigurasi wayar (2-wayar, 3-wayar, 4-wire) memainkan peranan penting dalam ketepatan pengukuran RTD.
- PLC disepadukan dengan lancar dengan penderia RTD, membolehkan pemantauan dan kawalan suhu yang canggih dalam sistem automasi.
- Penentukuran tetap dan amalan pemasangan yang betul adalah penting untuk mengekalkan ketepatan dan kebolehpercayaan penderia RTD.
Dengan memahami fungsi dan aplikasi RTD dan termokopel, profesional dalam sektor automasi industri boleh membuat keputusan termaklum untuk meningkatkan sistem pemantauan suhu mereka, memastikan kecekapan dan kebolehpercayaan dalam operasi mereka.
Mencari PLC baharu yang asli untuk projek anda? Di Kwoco, kami menyimpan PLC terkini daripada jenama terkenal seperti Omron, Mitsubishi, dan Schneider. Beli dengan yakin—penghantaran pantas, kualiti terjamin! Beli Sekarang
Hubungi Kami
Cuma isi nama, alamat e-mel dan penerangan ringkas tentang pertanyaan anda dalam borang ini. Kami akan menghubungi anda dalam masa 24 jam.
Anda Juga Mungkin Mendapatkan Topik Ini Menarik
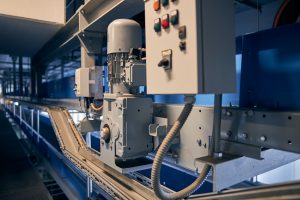
Kes Kerjasama dengan Pelanggan Amerika-OA 30 Syarat Pembayaran
Kes Kerjasama dengan Pelanggan Amerika-OA 30 Syarat Pembayaran Untuk meningkatkan kecekapan dan keberkesanan perkongsian kami, organisasi kami secara berterusan
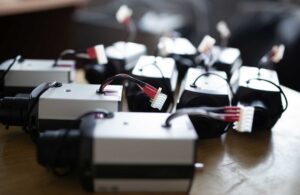
Adakah Servo Motors AC atau DC? Memahami Perbezaan
Satu soalan yang sering saya hadapi ialah, "Adakah motor servo AC atau DC?" Ia adalah titik kekeliruan yang biasa, dan memahami jawapannya adalah penting bagi sesiapa yang ingin melaksanakan motor servo dengan berkesan dalam sistem mereka. Mari selami topik ini untuk menjelaskan perbezaan dan membantu anda membuat keputusan termaklum untuk permohonan anda.
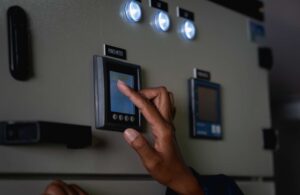
Input & Output Analog PLC: Panduan Pengujian & Penyelesaian Masalah
Pengawal Logik Boleh Aturcara (PLC) adalah tulang belakang kepada banyak sistem automasi industri. Ia membolehkan kawalan tepat ke atas mesin dan proses, bergantung pada input dan output (I/O) untuk berkomunikasi dengan peranti luaran.