Guida essenziale alla calibrazione dei sensori per la precisione industriale
In questa guida esploreremo i dettagli di sensore calibrazione, perché è importante, come viene documentata e i vari metodi utilizzati nei diversi tipi di sensori.
Sommario
Che cos'è la calibrazione del sensore?
La calibrazione del sensore comporta la regolazione di un sensore o di uno strumento di misurazione per ridurre o eliminare le imprecisioni nella misurazione. Con la calibrazione, i tecnici stabiliscono una relazione tra l'output del sensore e un riferimento standard, riducendo al minimo l'errore e assicurando che i dati di misurazione siano strettamente allineati alle condizioni effettive.
La calibrazione è spesso confusa con la regolazione, ma hanno scopi diversi. La calibrazione verifica quanto bene le misurazioni di un sensore siano confrontabili con standard noti, mentre la regolazione modifica attivamente il sensore per correggere eventuali discrepanze. Una calibrazione accurata è essenziale per mantenere risultati di misurazione precisi e riproducibili, che sono fondamentali per la garanzia della qualità nei processi industriali.
Perché la calibrazione dei sensori è essenziale?
L'importanza della calibrazione non può essere sopravvalutata. I sensori calibrati assicurano una misurazione precisa, portando a operazioni stabili ed efficienti in settori come la produzione, l'elaborazione chimica e la farmaceutica. Ecco perché la calibrazione è così importante:
- Garantisce la precisione della misurazione: La calibrazione verifica gli errori di misurazione che potrebbero essere derivati da condizioni ambientali o dalla deriva dell'attrezzatura nel tempo. Dati accurati significano un migliore controllo delle variabili di processo.
- Supporta la garanzia della qualità: La calibrazione è fondamentale per le aziende che si sforzano di soddisfare gli standard ISO e altri standard di qualità. Garantisce che le misurazioni aderiscano alle tolleranze richieste.
- Riduce i rischi per la sicurezza: Dati imprecisi dei sensori possono portare a decisioni di controllo errate, mettendo potenzialmente in pericolo il personale e le attrezzature.
Documentazione della taratura: il certificato di taratura
La documentazione di calibrazione fornisce la prova della calibrazione e registra i dati critici. Questa documentazione include un certificato o un rapporto di calibrazione, che verifica la tracciabilità rispetto a standard riconosciuti. I certificati di calibrazione spesso includono:
- Standard utilizzati: Gli standard di riferimento applicati nella calibrazione.
- Risultati della calibrazione: Specifiche, funzioni di calibrazione, curve, tabelle o diagrammi che rappresentano i dati di calibrazione.
- Incertezza di misura: I valori di incertezza associati alla calibrazione per indicare la precisione prevista.
Avere a portata di mano questa documentazione è essenziale per gli audit e il mantenimento dell'integrità dei processi.
Comprendere la ricalibrazione e la sua importanza
Nel tempo, la precisione del sensore può degradarsi a causa di usura, invecchiamento o cambiamenti ambientali. Una ricalibrazione regolare assicura che i sensori rimangano entro limiti di errore accettabili. Le aziende spesso seguono gli standard ISO 9001, che delineano i requisiti per il monitoraggio degli strumenti di misurazione e i programmi di ricalibrazione.
Stabilendo un processo di ricalibrazione di routine, le aziende possono impedire che la deriva influisca sulla qualità dei dati. Una calibrazione regolare riduce al minimo i tempi di inattività, migliora l'efficienza operativa e mantiene la conformità con gli standard di qualità.
Calibrazione dei sensori per diversi misurandi
La calibrazione varia a seconda del tipo di misurazione eseguita dal sensore, come pressione, forza o coppia. Ecco uno sguardo alla calibrazione tra diversi tipi di sensori:
- Calibrazione del sensore di pressione: Spesso ciò comporta l'applicazione di una pressione nota e la registrazione dell'output del sensore per stabilirne la precisione.
- Calibrazione del sensore di forza:I sensori di forza vengono calibrati con carichi applicati per verificare che forniscano misurazioni corrette in tutto il loro intervallo.
- Calibrazione del sensore di coppia: La calibrazione della coppia utilizza la forza rotazionale applicata per verificare che le misurazioni siano coerenti e accurate.
- Calibrazione dell'accelerometro:La calibrazione degli accelerometri richiede un movimento controllato per garantire che misurino l'accelerazione in modo accurato.
Ciascuno di questi metodi di calibrazione ha il proprio set di procedure e standard per garantire l'affidabilità della misurazione.
Cause comuni di errore del sensore
Diversi fattori possono introdurre errori nelle misurazioni dei sensori, influenzando potenzialmente il controllo del processo. Ecco i principali tipi di errore e come si verificano:
- Errore di riferimento zero: La deriva del punto zero del sensore può verificarsi a causa di influenze ambientali come variazioni di temperatura o pressione.
- Spostamento di gamma: Se non viene ricalibrato, l'intervallo operativo potrebbe cambiare, causando misurazioni imprecise del sensore.
- Usura o danni meccanici: Danni fisici o usura possono compromettere la capacità del sensore di effettuare misurazioni accurate, rendendo potenzialmente necessarie riparazioni o sostituzioni.
La comprensione di questi tipi di errore aiuta a diagnosticare i problemi di calibrazione e a stabilire routine di calibrazione efficaci.
Esecuzione di un controllo di calibrazione "come trovato"
Un controllo "as-found" è una calibrazione preliminare eseguita senza regolazioni. Aiuta a determinare se le letture correnti dello strumento rientrano in livelli di tolleranza accettabili. Il controllo viene eseguito in più punti lungo l'intervallo del sensore, spesso utilizzando un controllo "Five-Point" (0%, 25%, 50%, 75% e 100%).
Se le letture "come trovate" rientrano nella deviazione consentita, la calibrazione completa potrebbe non essere necessaria. In caso contrario, viene eseguita una calibrazione completa per riportare le letture entro i limiti di tolleranza.
Conclusione
La calibrazione dei sensori è un processo cruciale per mantenere l'accuratezza, la sicurezza e l'efficienza delle operazioni industriali. Calibrando e ricalibrando regolarmente i sensori, le industrie possono ridurre gli errori di misurazione, migliorare la garanzia della qualità e garantire la conformità agli standard internazionali.
La comprensione dei fondamenti della calibrazione, dalla documentazione alle cause degli errori e ai controlli di calibrazione, consente a ingegneri e tecnici di ottenere un controllo ottimale del processo.
Se stai cercando un fornitore affidabile di sensori industriali, contatta Kwoco. Forniamo sensori nuovi di zecca e originali di marchi affidabili come Omron E Chiave, disponibile per la spedizione in tutto il mondo.
Contattaci
Basta compilare il tuo nome, indirizzo email e una breve descrizione della tua richiesta in questo modulo. Ti contatteremo entro 24 ore.
Categoria di prodotto
Prodotti in saldo
Potresti trovare interessanti anche questi argomenti
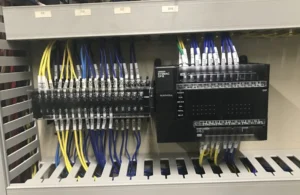
Guida semplice: collegamento del PLC Omron tramite Ethernet
Collegare un PLC Omron a Ethernet può sembrare complicato, ma in realtà è piuttosto semplice. Ti è mai capitato di trovarti in una situazione in cui il tuo progetto aveva urgente bisogno di connettività remota PLC, ma non sapevi da dove iniziare?
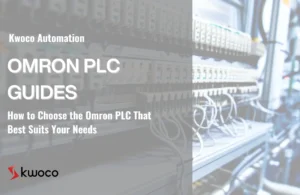
Come scegliere il PLC Omron più adatto alle tue esigenze
Come scegliere il PLC Omron più adatto alle tue esigenze Hai difficoltà a trovare il PLC giusto per le tue esigenze industriali?
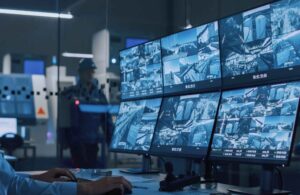
Che cosa è DCS? Una guida ai sistemi di controllo distribuiti
I Distributed Control Systems (DCS) hanno rivoluzionato il modo in cui le industrie gestiscono e controllano processi complessi. Questa guida completa approfondirà l'architettura, i vantaggi e le applicazioni dei DCS, spiegando perché comprendere questa tecnologia è essenziale per l'automazione e il controllo industriali moderni.