Guida PLC: concetti, applicazioni e fondamenti del cablaggio
Sommario
Introduzione: Il “cervello” nell’onda dell’automazione
Nell'attuale panorama in rapida evoluzione dell'automazione industriale, efficienza produttiva, flessibilità e affidabilità sono parametri essenziali per la capacità di produzione.
I tradizionali e complessi circuiti di controllo dei relè faticano a soddisfare le esigenze dell'industria moderna in termini di logica intricata, tempi di risposta rapidi e manutenzione agevole.
È in questo contesto che il Controllore Logico Programmabile (PLC) è emerso e si è rapidamente affermato come il "cervello" centrale dei sistemi di controllo dell'automazione.
Questo documento vi guiderà sistematicamente attraverso il mondo dei PLC, spiegandone i principi fondamentali, le ampie applicazioni e le tecniche di cablaggio essenziali.
Parte 1: Presentazione del PLC – Concetti fondamentali e vantaggi
1. Che cosa è un PLC?
Un PLC, o controllore logico programmabile, è un sistema elettronico digitale progettato specificamente per funzionare in ambienti industriali.
Utilizza una memoria programmabile per memorizzare istruzioni orientate all'utente per l'implementazione di funzioni quali operazioni logiche, controllo di sequenza, temporizzazione, conteggio e operazioni aritmetiche.
Tramite moduli di ingresso/uscita (I/O) digitali o analogici, controlla vari tipi di macchine o processi produttivi.
2. Confronto con il controllo tradizionale: perché scegliere un PLC?
Prima dell'adozione diffusa dei PLC, il controllo industriale si basava principalmente su circuiti logici cablati composti da relè, contattori, timer, ecc. Concettualmente:
- Circuiti tradizionali (logica a relè):
- Funzionalità fissa: Una volta cablata, la modifica della logica di controllo risulta difficile e richiede molto lavoro.
- Complessità del cablaggio: Il numero di componenti e la quantità di cablaggi aumentano esponenzialmente con la complessità della logica di controllo.
- Manutenzione difficile: La risoluzione dei problemi richiede un controllo punto per punto delle connessioni fisiche, il che richiede molto tempo.
- Contatti limitati: I contatti fisici hanno una quantità finita e limitazioni nella durata.
- Scarsa scalabilità: L'aggiunta di nuove funzioni spesso richiede una significativa riprogettazione e un nuovo cablaggio.
- Sistemi di controllo PLC:
- Elevata flessibilità: La logica di controllo risiede in un programma software. La modifica delle funzionalità in genere comporta solo la modifica del codice del programma, senza alterare il cablaggio hardware. Ad esempio, modificare il pulsante di ingresso X00 dal controllo dell'uscita Y001 al controllo di Y002 richiede solo una piccola modifica al software di programmazione.
- Design e cablaggio semplificati: Gli ingressi (ad esempio pulsanti, sensori) e le uscite (ad esempio lampade spia, bobine dei contattori del motore) si collegano direttamente ai moduli I/O del PLC, riducendo drasticamente la complessità del cablaggio esterno.
- Funzionalità potenti: I PLC offrono un ricco set di istruzioni, implementando facilmente logica complessa, temporizzazione, conteggio, manipolazione dei dati, ecc. I contatti software interni (normalmente aperti/normalmente chiusi) possono essere utilizzati praticamente senza limitazioni.
- Facilità di manutenzione e diagnostica: Il software di programmazione offre funzionalità di monitoraggio online, consentendo l'osservazione in tempo reale dello stato di esecuzione del programma e dei segnali I/O, facilitando la rapida localizzazione dei guasti.
- Elevata affidabilità e scalabilità: Progettati per ambienti industriali difficili, i PLC offrono un'elevata immunità ai disturbi. Il loro design modulare consente una facile espansione dei punti I/O o l'aggiunta di moduli funzionali specializzati in base all'evoluzione dei requisiti.
Tabella 1: Confronto tra sistemi PLC e sistemi di controllo relè tradizionali
Caratteristica | Sistema di controllo dei relè tradizionale | Sistema di controllo PLC |
---|---|---|
Implementazione della logica di controllo | Cablaggio hardware (cablato) | Programmazione software (programma software) |
Flessibilità/Modifica | Basso, richiede un nuovo cablaggio | Alto, modifica programma |
Complessità del sistema | Aumenta bruscamente con la scala | Principalmente nel software, l'hardware è più semplice |
Affidabilità | Contatti soggetti a usura, sensibili all'ambiente | Design industriale elevato, immune al rumore |
Manutenzione/Diagnostica | Difficile, tracciare i fili fisici | Più semplice, tramite il monitoraggio online del software |
Funzionalità | Logica di base, tempismo, conteggio | Logica complessa, matematica, comunicazioni, controllo avanzato |
Dimensioni fisiche | Più grande | Relativamente compatto |
Standardizzazione | Basso | Standard elevati e comuni a tutti i marchi |
Costo (sistema semplice) | Potenzialmente inferiore | Potenzialmente più alto |
Costo (sistema complesso) | Alto | Relativamente più basso |
Parte 2: Funzioni principali e domini applicativi dei PLC
Le capacità dei PLC vanno ben oltre il semplice controllo della commutazione. I PLC moderni sono dispositivi versatili e potenti, con applicazioni generalmente classificate in queste cinque aree:
- Controllo digitale (controllo discreto): Questa è l'applicazione PLC più fondamentale e diffusa. Comprende l'elaborazione di segnali ON/OFF (ingressi digitali) provenienti da dispositivi come pulsanti, interruttori e sensori, e il pilotaggio di attuatori come spie luminose, relè ed elettrovalvole (uscite digitali) in base alla logica di programma. Questo costituisce la base per le sequenze di avvio/arresto e le operazioni sequenziali delle apparecchiature.
- Controllo del movimento: Molti PLC, in particolare i modelli di fascia media e alta, sono dotati di uscite a impulsi ad alta velocità. Queste uscite generano treni di impulsi ad alta frequenza per controllare con precisione motori passo-passo o servoazionamenti, consentendo attività complesse come il posizionamento di precisione, il controllo della velocità e l'inseguimento della traiettoria. Questo è fondamentale per macchinari per imballaggio, macchine CNC, robotica e applicazioni simili.
- Controllo analogico: I processi industriali spesso comportano grandezze fisiche che variano in modo continuo, come temperatura, pressione, portata e livello. I PLC utilizzano moduli di ingresso analogico per acquisire segnali (tipicamente 4-20 mA o 0-10 V) da trasmettitori e sensori. Dopo l'elaborazione interna (conversione A/D, filtraggio, scalatura), i moduli di uscita analogica controllano dispositivi come valvole modulanti o azionamenti a frequenza variabile (VFD).VFD) per ottenere un controllo a circuito chiuso. Esempi comuni includono la regolazione della temperatura e l'approvvigionamento idrico a pressione costante. Molti PLC incorporano blocchi funzionali di controllo PID (Proporzionale-Integrale-Derivativo) per un controllo preciso del processo. Scopri di più sui controllori PID
- Trattamento dei dati (Elaborazione dati): I PLC possiedono solide capacità per operazioni matematiche (addizione, sottrazione, moltiplicazione, divisione, funzioni trigonometriche, ecc.), operazioni logiche, confronto dati, trasferimento dati e ordinamento. Possono raccogliere dati di produzione per l'analisi, l'elaborazione e l'archiviazione. Alcuni esempi includono il conteggio dei prodotti, il calcolo dei tempi di ciclo, la gestione delle ricette e l'implementazione di logiche di flusso di lavoro complesse (ad esempio, sistemi di gestione delle code).
- Comunicazione e networking: L'automazione moderna enfatizza l'interconnettività. I PLC sono dotati di diverse porte di comunicazione (ad esempio, RS232, RS485, Ethernet) e supportano diversi protocolli industriali (ad esempio, Modbus, Profibus, ProfiNet, EtherNet/IP). Ciò consente ai PLC di:
- Comunicare con le interfacce uomo-macchina (HMI (Interfaccia uomo-macchina))/Schermate touch: Creare interfacce grafiche per monitorare lo stato del dispositivo, impostare parametri e operazioni manuali, sostituendo numerosi pulsanti fisici e spie.
- Comunicare con i computer di supervisione/sistemi SCADA: Facilitare l'acquisizione dei dati, il monitoraggio remoto e la gestione degli impianti.
- Rete con altri PLC o dispositivi intelligenti (come VFD, strumenti): Costruire sistemi di controllo distribuito (DCS) o abilitare il funzionamento coordinato tra macchine.
- Esplora i protocolli industriali comuni: Modbus Organization, ODVA (gestisce EtherNet/IP et al.)
Parte 3: Fondamenti del cablaggio PLC
Un cablaggio corretto è fondamentale per il funzionamento stabile di qualsiasi sistema PLC. Il cablaggio del PLC riguarda principalmente i terminali di ingresso e di uscita.
1. Cablaggio di ingresso: Gli ingressi PLC ricevono segnali da dispositivi di campo esterni.
- Dispositivi collegabili: Pulsanti, selettori, finecorsa, sensori di prossimità (induttivi), sensori fotoelettrici, interruttori magnetici (interruttori reed, spesso per la posizione del cilindro), amplificatori in fibra ottica, sensori a U (a fessura), ecc. Fondamentalmente, questi dispositivi forniscono un segnale di commutazione al PLC.
- Elementi base del circuito: Un circuito di input completo richiede una fonte di alimentazione, un elemento di commutazione (il dispositivo di input) e il carico (in questo caso, l'optoaccoppiatore del punto di input del PLC).
- Tipi di ingresso e collegamento (esempio: Mitsubishi FX3U, alimentazione DC24V):
- Terminale comune (S/S o COM): Gli ingressi del PLC sono in genere isolati internamente tramite optoisolatori. Un lato di tutti gli optoisolatori di ingresso è collegato internamente a un terminale comune. Per il cablaggio esterno, questo terminale comune deve essere collegato a un polo dell'alimentatore CC esterno.
- Ingresso sink (logica NPN): Il terminale comune (S/S) è collegato al polo positivo (+24 V) dell'alimentatore CC esterno. Il dispositivo di input (ad esempio, un pulsante) si collega tra il terminale di ingresso X del PLC e il polo negativo (0 V) dell'alimentatore. Quando il pulsante viene premuto, la corrente fluisce da +24 V -> S/S -> optoaccoppiatore interno -> terminale X -> pulsante -> 0 V, completando il circuito, e il PLC registra un ingresso ON. Questa configurazione è utilizzata per i sensori di tipo NPN.
- Input sorgente (logica PNP): Il terminale comune (S/S) è collegato al polo negativo (0 V) dell'alimentatore CC esterno. Il dispositivo di input si collega tra il terminale di ingresso X del PLC e il polo positivo (+24 V) dell'alimentatore. Quando si preme il pulsante, la corrente fluisce da +24 V -> pulsante -> terminale X -> optoaccoppiatore interno -> S/S -> 0 V. Questa configurazione è utilizzata per i sensori di tipo PNP.
- Collegamento del dispositivo a 2 fili: Dispositivi come pulsanti standard, finecorsa e interruttori magnetici a 2 fili vengono collegati in base allo schema di cablaggio Sink o Source selezionato. Nota: gli interruttori magnetici a 2 fili spesso presentano polarità (fili marrone e blu). Collegare correttamente in base al tipo di ingresso del PLC (Sink/Source) e al flusso di corrente. Regola generale: per l'ingresso Sink (S/S a +24 V), collegare il filo marrone all'ingresso X e il filo blu a 0 V. Per l'ingresso Source (S/S a 0 V), collegare il filo marrone a +24 V e il filo blu all'ingresso X. (Verificare sempre le specifiche del dispositivo).
- Collegamento del sensore a 3 fili (ad esempio, fotoelettrico/di prossimità):
- Sensore NPN: Filo marrone a +24 V, filo blu a 0 V, filo del segnale nero al terminale di ingresso X del PLC. L'ingresso del PLC dovere essere configurato/cablato per ingresso Sink (S/S collegato a +24 V).
- Sensore PNP: Filo marrone a +24 V, filo blu a 0 V, filo del segnale nero al terminale di ingresso X del PLC. L'ingresso del PLC dovere essere configurato/cablato per l'ingresso sorgente (S/S collegato a 0 V).
2. Cablaggio di uscita: Le uscite PLC pilotano carichi esterni.
- Carichi collegabili: Spie luminose, elettrovalvole (per controllo pneumatico/idraulico), relè di interposizione, contattori (per motori ad alta potenza), stato solido Relè (SSR, per riscaldatori, ecc.), segnali di controllo per VFD, stepper/servoazionamenti, ecc.
- Tipi di output: I moduli di uscita PLC sono disponibili principalmente in tre tipologie, scelte in base alle caratteristiche del carico e alle esigenze dell'applicazione.
- Uscita relè (ad esempio, suffisso MR in Mitsubishi):
- Principio: utilizza relè elettromeccanici miniaturizzati interni. Quando il programma eccita una bobina di uscita (Y), il contatto del relè interno corrispondente si chiude, completando il circuito di carico esterno.
- Vantaggi: può pilotare carichi sia CA che CC, ampio intervallo di tensione, capacità di corrente relativamente elevata, buon isolamento elettrico, costo inferiore.
- Svantaggi: durata meccanica limitata (in genere da centinaia di migliaia a milioni di cicli), bassa velocità di commutazione (~10 ms), non adatto per commutazione ad alta frequenza (come PWM o uscite a impulsi ad alta velocità). Frequenza di commutazione consigliata inferiore a ~0,1 Hz (6 volte/minuto) per massimizzare la durata.
- Cablaggio: Ogni punto di uscita (o gruppo) ha un terminale comune (COM). Collegare un lato del carico al terminale di uscita Y, l'altro lato a un polo dell'alimentatore del carico. Collegare l'altro polo dell'alimentatore del carico al corrispondente terminale COM. Il collegamento COM è flessibile in termini di polarità (CC) o fase/neutro (CA).
- Uscita a transistor (ad esempio, suffisso MT in Mitsubishi):
- Principio: utilizza transistor di potenza interni (tipicamente MOSFET).
- Vantaggi: velocità di commutazione estremamente elevata (microsecondi), nessuna usura meccanica, durata molto lunga, ideale per applicazioni ad alta frequenza come il pilotaggio di servoazionamenti/passo-passo (uscite a impulsi) e controllo PWM (dimmeraggio/velocità).
- Svantaggi: Può pilotare solo carichi in corrente continua. Minore tolleranza ai sovraccarichi e alle correnti di spunto; spesso è necessaria una protezione esterna (ad esempio, un diodo flyback per carichi induttivi). Presenta una bassa corrente di dispersione quando è spento.
- Cablaggio: disponibile nei tipi Sink (NPN) o Source (PNP).
- Uscita del dissipatore: Il terminale comune (COM) si collega al polo negativo (0 V) dell'alimentatore del carico esterno. Collegare un lato del carico al polo positivo (+V) dell'alimentatore, l'altro lato al terminale di uscita Y del PLC. Quando Y si attiva, collega il carico a 0 V.
- Output sorgente: Il terminale comune (COM) si collega al polo positivo (+V) dell'alimentatore del carico esterno. Collegare un lato del carico al polo negativo (0V) dell'alimentatore, l'altro lato al terminale di uscita Y del PLC. Quando Y si attiva, fornisce +V al carico.
- Uscita Triac (uscita Tiristore, ad esempio suffisso MS in Mitsubishi):
- Principio: utilizza triac interni (un tipo di tiristore bidirezionale).
- Vantaggi: elevata velocità di commutazione, lunga durata, adatto per azionare carichi CA, in particolare piccoli contattori CA, elettrovalvole, ecc.
- Svantaggi: Può pilotare solo carichi CA. In genere è dotato di commutazione a passaggio per lo zero (un vantaggio per la riduzione del rumore, ma impedisce il controllo dell'angolo di fase). Presenta una certa corrente di dispersione quando è spento. Suscettibile a danni da picchi/sovratensioni di tensione.
- Cablaggio: concetto simile al cablaggio di uscita del relè (carico collegato tra Y e alimentazione, COM collegato all'altro lato dell'alimentazione), ma esclusivamente per circuiti CA.
- Uscita relè (ad esempio, suffisso MR in Mitsubishi):
Tabella 2: Confronto dei tipi di moduli di uscita PLC
Caratteristica | Tipo di relè (MR) | Tipo di transistor (MT) | Tipo Triac (MS) |
---|---|---|---|
Tipo di carico guidato | CA / CC | Solo DC | Solo aria condizionata |
Velocità di commutazione | Lento (~10 ms) | Molto veloce (<1 ms) | Veloce (<1 ms) |
Frequenza di commutazione | Basso (<0,1 Hz consigliato) | Molto alto (gamma kHz) | Relativamente alto |
Durata | Limitato (meccanico) | Lungo (stato solido) | Lungo (stato solido) |
Capacità attuale | Più alto (ad esempio, 2A) | Inferiore (ad esempio, 0,5 A) | Moderato (ad esempio, 0,5-1A) |
Isolamento | Buono (divario fisico) | Tipicamente optoisolato | Tipicamente optoisolato |
Tolleranza alle sovratensioni | Meglio | Inferiore, richiede protezione | Inferiore, richiede protezione |
Alimentazione esterna richiesta. | Il circuito di carico necessita della propria alimentazione CA/CC | Il circuito di carico necessita della propria alimentazione CC | Il circuito di carico necessita della propria alimentazione CA |
Applicazione tipica | Contattori, Solenoidi, Lampade | Impulsi ad alta velocità (movimento), SSR, LED | Solenoidi CA, piccoli carichi CA |
Guida alla selezione:
- Se il carico è CA o CC e la frequenza di commutazione è bassa (ad esempio, inferiore a 6 volte al minuto), l'uscita a relè è spesso la scelta preferita per semplicità e convenienza.
- Se è richiesta una commutazione ad alta velocità, la generazione di impulsi in uscita (per il controllo del movimento) o la commutazione frequente di carichi CC, è necessaria l'uscita a transistor. Ricordarsi di selezionare Sink (NPN) o Source (PNP) in base al design del sistema e al tipo di sensore.
- Se il carico è in corrente alternata e richiede una commutazione più rapida rispetto ai relè o un funzionamento molto frequente, è possibile prendere in considerazione l'uscita Triac.
Conclusione:
Il controllore logico programmabile (PLC), con la sua intrinseca flessibilità, le potenti funzionalità, la facilità di programmazione e manutenzione e l'eccezionale affidabilità, rappresenta un componente fondamentale indispensabile nel campo del controllo dell'automazione industriale moderno.
Le sue applicazioni spaziano dal controllo logico digitale fondamentale al controllo sofisticato del movimento, alla regolazione analogica precisa, all'elaborazione dati avanzata e alla comunicazione di rete senza interruzioni, permeando linee di produzione automatizzate e apparecchiature in diversi settori.
Comprendere i concetti fondamentali dei PLC, familiarizzare con le loro diverse capacità e padroneggiare le corrette tecniche di cablaggio di input/output (in particolare distinguendo tra Sink/Source, NPN/PNP e selezionando il tipo di output appropriato) sono competenze essenziali per ogni ingegnere e tecnico dell'automazione.
Con la continua evoluzione dell'Industria 4.0 e della produzione intelligente, i PLC manterranno il loro ruolo fondamentale, consentendo alle aziende di ottenere una produzione più efficiente, intelligente e flessibile.
Dai potenza ai tuoi progetti con i nuovi PLC originali Omron, Mitsubishi e Schneider, disponibili in magazzino e pronti da subito!
Contattaci
Basta compilare il tuo nome, indirizzo email e una breve descrizione della tua richiesta in questo modulo. Ti contatteremo entro 24 ore.
Categoria di prodotto
Prodotti in saldo
Potresti trovare interessanti anche questi argomenti
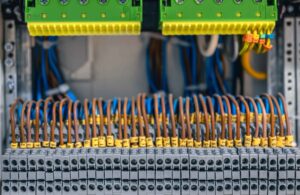
Risoluzione dei problemi comuni dei guasti dei PLC: una guida ai controllori logici programmabili
I controllori logici programmabili (PLC) sono la spina dorsale dell'automazione moderna, orchestrando il funzionamento senza soluzione di continuità di macchinari e processi industriali. Tuttavia, come qualsiasi tecnologia, possono incontrare problemi che interrompono le operazioni.
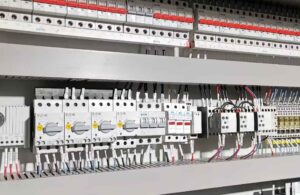
Sensore di prossimità vs sensore fotoelettrico
Questo articolo si addentra nell'affascinante regno dei sensori di prossimità e dei sensori fotoelettrici, esplorandone funzionalità, differenze e applicazioni. Che tu sia un ingegnere esperto in una fabbrica di macchinari e attrezzature o un fornitore di soluzioni alla ricerca dei migliori componenti di automazione, comprendere questi tipi di sensori è fondamentale. Come stabilimento di produzione di prodotti di controllo e automazione industriale, siamo qui per illuminare le complessità di questi componenti vitali, guidandoti infine verso decisioni informate per i tuoi progetti.
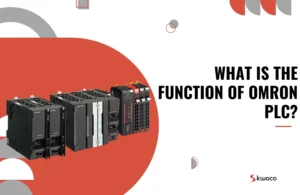
Qual è la funzione del PLC Omron?
Qual è la funzione di Omron PLC? Sei stanco di avere a che fare con sistemi di controllo inaffidabili che causano ritardi e