Introduzione ai controllori logici programmabili: il tuo gateway per l'automazione industriale
Sommario
1. Che cos'è un PLC (controllore logico programmabile)?
Un controllore logico programmabile (PLC) è un computer industriale specializzato progettato per automatizzare i processi industriali. Il primo PLC è stato sviluppato per sostituire i sistemi logici a relè cablati, offrendo una soluzione più flessibile ed efficiente.
Vedo i PLC come il cervello dietro molti sistemi automatizzati in fabbriche e impianti. Prendono input da vari dispositivi come sensori e interruttori, elaborano le informazioni in base a un programma PLC e generano output per controllare macchinari e attrezzature.
I PLC sono ampiamente utilizzati nell'automazione industriale per la loro robustezza, affidabilità e capacità di resistere ad ambienti industriali difficili. Sono progettati per controllare e monitorare i processi con elevata precisione, migliorando l'efficienza e riducendo l'errore umano.
Come esperto di automazione industriale, ho visto come i PLC hanno rivoluzionato la produzione, consentendo lo svolgimento fluido di operazioni complesse. Il controller digitale modulare è dotato di una memoria programmabile per l'archiviazione di istruzioni ed esecuzione di funzioni per il controllo di macchine e processi.
2. Come funziona un PLC?
Un PLC opera in un ciclo continuo, scansionando il suo programma e aggiornando gli output in base agli input correnti. Questo processo comporta la lettura dello stato di input, l'esecuzione della logica di controllo scritta nel linguaggio di programmazione e quindi l'aggiornamento dello stato di output di conseguenza. Il PLC riceve segnali dai dispositivi di input e prende decisioni in base alla logica programmata.
Il lavoro del PLC ruota attorno all'elaborazione delle informazioni e alla presa di decisioni in tempo reale. Ad esempio, se un sensore rileva un prodotto su un nastro trasportatore, il PLC può attivare un attuatore per spostare il prodotto alla fase successiva.
Trovo che la capacità dei PLC di elaborare informazioni in modo rapido e accurato sia ciò che li rende così preziosi nell'automazione industriale. La CPU (Central Processing Unit) è il componente principale che esegue il programma e prende queste decisioni.
3. Quali sono i componenti di base di un PLC?
I componenti di base di un PLC includono la CPU (Central Processing Unit), moduli di input e output, alimentatori e un dispositivo di programmazione. La CPU è il cervello del PLC, esegue il programma ed elabora i dati. I moduli di input ricevono segnali da dispositivi esterni, mentre i moduli di output inviano segnali di controllo alla macchina.
Componente | Descrizione |
---|---|
processore | Esegue il programma ed elabora i dati. |
Modulo di ingresso | Riceve segnali da dispositivi esterni. |
Modulo di uscita | Invia segnali di controllo ai macchinari. |
Alimentatori | Fornisce alimentazione ai componenti PLC. |
Dispositivo di programmazione | Utilizzato per creare e modificare programmi PLC. |
Nella mia esperienza, comprendere questi componenti è fondamentale per chiunque lavori con i PLC. Ad esempio, il modulo di input può essere digitale o analogico, a seconda del tipo di segnale che riceve. Allo stesso modo, i moduli di output possono controllare vari dispositivi, come motori, valvole e luci.
4. Quali sono i diversi tipi di PLC?
Esistono principalmente due tipi di PLC: compatti e modulari. I PLC compatti sono unità all-in-one con ingressi e uscite integrati, adatti per applicazioni su piccola scala. I PLC modulari, d'altro canto, sono costituiti da moduli separati che possono essere configurati ed espansi a seconda delle necessità.
I PLC modulari offrono maggiore flessibilità, consentendo agli utenti di personalizzare il sistema in base alle loro specifiche esigenze. Spesso consiglio i PLC modulari per sistemi complessi in cui la scalabilità è importante. Ad esempio, un PLC modulare potrebbe includere moduli separati per ingressi digitali, ingressi analogici, uscite digitali e uscite analogiche, ciascuno su misura per diversi tipi di sensori e attuatori.
5. Come si esegue la programmazione PLC?
La programmazione PLC implica la creazione di un set di istruzioni che indicano al PLC come operare. Ciò avviene in genere tramite software di programmazione specializzato fornito dal produttore del PLC, il PLC prende queste istruzioni e le esegue in sequenza. La programmazione di un PLC richiede la comprensione del processo che viene automatizzato e della logica di controllo desiderata.
Il linguaggio di programmazione per i PLC può variare, ma il più comune è la logica ladder, un linguaggio grafico che assomiglia ai diagrammi logici dei relè. Altri linguaggi di programmazione per PLC includono il diagramma a blocchi funzionali (FBD), il testo strutturato (ST) e il diagramma funzionale sequenziale (SFC). Nel mio lavoro, ho scoperto che la logica ladder è spesso preferita per la sua semplicità e facilità di comprensione, specialmente per i tecnici che hanno familiarità con la logica dei relè.
6. Quali sono i linguaggi di programmazione PLC più comuni?
I linguaggi di programmazione PLC offrono diversi modi per creare programmi di controllo. La logica ladder è il linguaggio di programmazione PLC più ampiamente utilizzato, noto per la sua rappresentazione visiva della logica dei relè. Il diagramma a blocchi funzionali (FBD) è un altro linguaggio grafico che utilizza blocchi per rappresentare funzioni e le loro interconnessioni.
Il testo strutturato (ST) è un linguaggio di alto livello simile al Pascal, che offre capacità di programmazione più avanzate. Il diagramma di funzione sequenziale (SFC) è utilizzato per processi complessi che coinvolgono più passaggi e transizioni. Ho utilizzato tutti questi linguaggi in vari progetti e apprezzo la flessibilità che offrono. Ad esempio, il testo strutturato è eccellente per calcoli complessi, mentre la logica ladder è ideale per un semplice controllo on/off.
- Logica a gradini: assomiglia agli schemi logici dei relè elettrici, rendendolo intuitivo per chi ha familiarità con i sistemi elettrici.
- Diagramma a blocchi funzionali (FBD): utilizza blocchi grafici per rappresentare funzioni, adatto per logiche complesse.
- Testo strutturato (ST): linguaggio di alto livello simile al Pascal, utilizzato per attività di programmazione avanzate.
- Diagramma funzionale sequenziale (SFC): ideale per processi con più fasi e transizioni.
7. Che cos'è la logica ladder e come viene utilizzata nella programmazione PLC?
La logica ladder è un linguaggio di programmazione grafico che rappresenta la logica di controllo in un modo che ricorda i diagrammi logici dei relè elettrici. Utilizza contatti e bobine per rappresentare rispettivamente input e output. La logica ladder è ampiamente utilizzata perché è facile da comprendere e visualizzare.
Nella logica ladder, un rung rappresenta una singola istruzione di controllo, con contatti sulla sinistra (input) e bobine sulla destra (output). Il PLC esegue ogni rung in sequenza, aggiornando gli output in base allo stato degli input. Spesso utilizzo la logica ladder per semplici attività di controllo, come l'avvio e l'arresto di motori o il controllo di luci. Ad esempio, un semplice rung potrebbe controllare se è premuto un pulsante di avvio (input) e quindi eccitare un motore (output).
Ecco un semplice esempio di un gradino della logica ladder:
Pulsante di avvio (ingresso) –| |– Motore (uscita)
8. Come si interfacciano i PLC con altri dispositivi e sistemi?
I PLC possono interfacciarsi con un'ampia gamma di dispositivi e sistemi utilizzando vari protocolli di comunicazione. I moduli di input e output consentono ai PLC di connettersi a sensori, attuatori e altri dispositivi di campo. I PLC possono anche comunicare con altri PLC, HMI (Human Machine Interfaces) e sistemi SCADA (Supervisory Control and Data Acquisition).
Ad esempio, un PLC potrebbe usare Modbus per comunicare con un modulo I/O remoto o EtherNet/IP per connettersi a un sistema SCADA. Ho lavorato a progetti in cui i PLC erano integrati in reti industriali Internet of Things (IIoT) più grandi, consentendo il monitoraggio e il controllo remoti. Le capacità di interfaccia dei PLC sono fondamentali per la creazione di sistemi di automazione interconnessi e intelligenti.
9. Quali sono le applicazioni dei PLC nell'automazione industriale?
Le applicazioni PLC sono vaste e variegate, e abbracciano diversi settori e processi. I PLC sono utilizzati per automatizzare tutto, dalle macchine semplici alle linee di produzione complesse. Alcune applicazioni PLC comuni includono il controllo di sistemi di trasporto, la gestione di sistemi HVAC, l'azionamento di macchine per l'imballaggio e il monitoraggio di processi industriali.
Nella mia esperienza, i PLC sono particolarmente utili in applicazioni che richiedono elevata affidabilità e precisione. Ad esempio, in un impianto di lavorazione alimentare, un PLC può controllare la temperatura, la pressione e la portata degli ingredienti per garantire una qualità costante del prodotto. I PLC possono anche essere utilizzati in applicazioni critiche per la sicurezza, come i sistemi di arresto di emergenza, dove la loro affidabilità è fondamentale. Utilizzati per controllare un'ampia varietà di macchine e processi, assicurandone il corretto ed efficiente funzionamento.
Ecco alcuni esempi di applicazioni PLC:
- Sistemi di trasporto
- Sistemi HVAC
- Macchine per l'imballaggio
- Braccia robotiche
- Impianti di trattamento delle acque
- Sistemi di arresto di emergenza
10. Come risolvere i problemi dei sistemi PLC?
La risoluzione dei problemi dei sistemi PLC comporta l'identificazione e la risoluzione dei problemi che impediscono al sistema di funzionare correttamente. I problemi comuni includono input o output difettosi, errori di programmazione e guasti di comunicazione. Una risoluzione dei problemi efficace richiede un approccio sistematico e una buona comprensione del sistema PLC.
Inizio sempre controllando gli indicatori diagnostici e i registri degli errori del PLC. La maggior parte dei PLC ha una diagnostica integrata che può fornire informazioni preziose sullo stato del sistema. Poi verifico gli input e gli output usando un multimetro o un dispositivo di programmazione per assicurarmi che funzionino correttamente. Se il problema persiste, rivedo il programma del PLC per errori o incongruenze.
Ecco alcuni suggerimenti per la risoluzione dei problemi dei sistemi PLC:
- Controllare gli indicatori diagnostici e i registri degli errori del PLC.
- Verificare gli ingressi e le uscite utilizzando un multimetro.
- Controllare il programma PLC per individuare eventuali errori.
- Controllare che non vi siano collegamenti allentati o cavi danneggiati.
- Assicurarsi che l'alimentazione elettrica sia stabile.
- Testare i collegamenti di comunicazione con altri dispositivi.
Domande frequenti
Sebbene sia i PLC che i microcontrollori siano utilizzati per applicazioni di controllo, differiscono nella progettazione e nell'uso previsto. I PLC sono progettati per ambienti industriali, offrendo robustezza, affidabilità e facilità di programmazione. I microcontrollori, d'altro canto, sono in genere utilizzati nei sistemi embedded e nell'elettronica di consumo. Raccomando spesso i PLC per applicazioni industriali per la loro durata superiore e le caratteristiche specializzate.
Sì, i PLC possono essere utilizzati per l'automazione domestica, ma sono generalmente eccessivi per tali applicazioni. I sistemi di automazione domestica in genere utilizzano soluzioni più semplici e convenienti, come hub per la casa intelligente e microcontrollori. Tuttavia, per progetti di automazione domestica complessi o su larga scala, un PLC potrebbe essere un'opzione praticabile.
La logica ladder offre diversi vantaggi, tra cui la semplicità, la facilità di comprensione e la rappresentazione visiva della logica di controllo. È particolarmente utile per i tecnici che hanno familiarità con la logica dei relè elettrici, rendendo più semplice la transizione alla programmazione PLC. Trovo che la logica ladder sia una scelta eccellente per attività di controllo da semplici a moderatamente complesse.
La scelta del PLC giusto dipende da diversi fattori, tra cui la complessità dell'applicazione, il numero di input e output, la velocità di elaborazione richiesta e le esigenze di comunicazione. Consiglio di iniziare definendo i requisiti specifici della tua applicazione e quindi di selezionare un PLC che soddisfi tali esigenze. Considera fattori come scalabilità, supporto del linguaggio di programmazione e condizioni ambientali.
I sistemi SCADA (Supervisory Control and Data Acquisition) sono utilizzati per monitorare e controllare i processi industriali da una posizione centrale. Spesso funzionano insieme ai PLC, fornendo un'interfaccia di livello superiore per operatori e manager. I sistemi SCADA possono raccogliere dati da più PLC, visualizzare informazioni di processo in tempo reale e consentire agli operatori di apportare modifiche o impartire comandi. Considero SCADA uno strumento essenziale per la gestione di sistemi di automazione complessi, che fornisce preziose informazioni e capacità di controllo.
Dai potenza ai tuoi progetti con i nuovissimi servo Omron, Mitsubishi e Schneider originali, disponibili subito in magazzino!
Conclusione
- I PLC sono componenti essenziali dei moderni sistemi di automazione industriale.
- Per un'automazione efficace è fondamentale conoscere i diversi tipi di PLC e i loro linguaggi di programmazione.
- La logica a scala continua a essere una scelta popolare per la programmazione dei PLC grazie alla sua semplicità e facilità d'uso.
- I PLC possono interfacciarsi con un'ampia gamma di dispositivi e sistemi, consentendo soluzioni di automazione complesse.
- La risoluzione dei problemi dei sistemi PLC richiede un approccio sistematico e una buona conoscenza dei componenti e della programmazione del sistema.
- La scelta del PLC giusto dipende dai requisiti specifici dell'applicazione.
- Puoi familiarizzare con il mondo dei controllori logici programmabili esplorando Mitsubishi PLC, PLC Schneider, E Interfaccia utente Mitsubishi per comprendere le loro capacità e come possono migliorare l'automazione industriale.
- Per esigenze di automazione più avanzate, l'integrazione Servo delta E Inverter Schneider può garantire un controllo preciso e l'efficienza energetica dei vostri sistemi.
- Conoscendo e utilizzando queste tecnologie, puoi migliorare significativamente l'efficienza e la produttività dei tuoi processi industriali.
Sfruttando la mia competenza nei prodotti di controllo e automazione industriale, il mio obiettivo è fornire soluzioni che soddisfino le esigenze delle fabbriche di macchinari e attrezzature, dei produttori e delle aziende di soluzioni di fabbrica.
Il mio obiettivo è aiutarti a raggiungere un'automazione senza soluzione di continuità, migliorare la produttività e guidare il successo nelle tue operazioni. Contattami oggi stesso per saperne di più su come possiamo trasformare i tuoi processi industriali con soluzioni PLC avanzate.
Contattaci
Basta compilare il tuo nome, indirizzo email e una breve descrizione della tua richiesta in questo modulo. Ti contatteremo entro 24 ore.
Categoria di prodotto
Prodotti in saldo
Potresti trovare interessanti anche questi argomenti
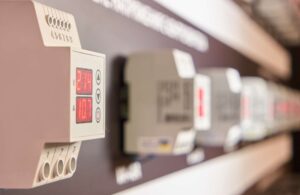
Comprensione del tempo di ciclo del PLC: ottimizza la tua automazione
Hai mai pensato a quanto velocemente il tuo sistema di automazione risponde ai cambiamenti? Il segreto sta nel tempo di ciclo del PLC, il battito cardiaco del tuo sistema di controllo. Comprendere questo concetto è fondamentale per chiunque sia coinvolto nell'automazione. In questo articolo, sveleremo cos'è il tempo di ciclo del PLC, perché è importante e come influisce sulle tue operazioni.
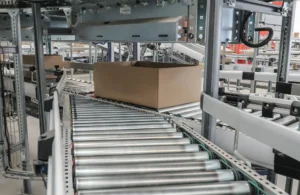
Cosa rilevano i sensori fotoelettrici?
Potresti chiederti: cosa rilevano esattamente i sensori fotoelettrici?
In parole povere, i sensori fotoelettrici rilevano la presenza o l'assenza di un oggetto tramite la luce. Sono componenti essenziali nell'automazione, utilizzati in tutti i settori per garantire che i processi funzionino senza intoppi ed efficientemente.
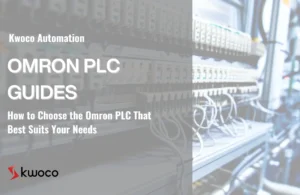
Come scegliere il PLC Omron più adatto alle tue esigenze
Come scegliere il PLC Omron più adatto alle tue esigenze Hai difficoltà a trovare il PLC giusto per le tue esigenze industriali?