Errori comuni e risoluzione dei problemi dei PLC Omron
Sommario
Il funzionamento stabile di questi sistemi è direttamente correlato all'efficienza produttiva, alla qualità del prodotto e ai costi operativi. Pertanto, la capacità di diagnosticare e risolvere rapidamente e accuratamente i problemi è fondamentale. PLC difetti è essenziale per mantenere la competitività di base di un'azienda.
Questo documento descrive sistematicamente le procedure e le tecniche di risoluzione dei problemi basate su principi comuni PLC di Omron scenari applicativi.
1. Sistema di alimentazione: il fondamento del funzionamento stabile del PLC
Un'alimentazione affidabile è il prerequisito fondamentale per il normale funzionamento del PLC. Le interruzioni dell'alimentazione spesso portano all'arresto immediato e completo del sistema.
- Fenomeni comuni: Il PLC non si accende completamente (nessun indicatore acceso) oppure presenta uno stato anomalo all'accensione (ad esempio, il LED ERROR è costantemente acceso o lampeggiante).
- Analisi approfondita delle cause:
- Alimentazione esterna: La tensione di ingresso fluttua oltre l'intervallo di tolleranza specificato dal PLC (in genere ±10% o ±15%, consultare il manuale hardware specifico), terminali di cablaggio allentati o ossidati che causano un'elevata resistenza di contatto oppure cavi di alimentazione danneggiati.
- Modulo di alimentazione PLC: Guasto o degrado dei componenti interni (ad esempio, fusibili, condensatori, circuiti integrati dei regolatori di tensione). Per i PLC modulari, anche un contatto difettoso tra il modulo di alimentazione e il backplane può causare problemi.
- Strategia efficiente per la risoluzione dei problemi:
- Verifica potenza in ingresso: Utilizzare un multimetro calibrato per misurare con precisione la tensione ai terminali di ingresso del modulo di alimentazione del PLC. Assicurarsi che la tensione sia stabile e rientri nell'intervallo specificato nella scheda tecnica.
- Ispezionare le connessioni fisiche: Verificare che tutti i collegamenti elettrici siano sicuri, correttamente terminati e privi di cortocircuiti o interruzioni. Verificare l'integrità di spine e prese di corrente.
- Eliminare le interferenze esterne: Verificare se apparecchiature ad alta potenza che si collegano ciclicamente sulla stessa linea elettrica causano disturbi. Se necessario, valutare l'installazione di un filtro di linea o di uno stabilizzatore/regolatore di tensione.
- Test di sostituzione del modulo: Se sono disponibili pezzi di ricambio, sostituire il modulo di alimentazione esistente con un modello identico per isolare se il guasto risiede nel modulo stesso. Fare riferimento a Sito ufficiale di Omron per informazioni e specifiche sui moduli compatibili.
2. Canali di input/output (I/O): il ponte verso i dispositivi di campo
I moduli I/O gestiscono lo scambio di segnali tra il PLC e i dispositivi di campo come sensori e attuatori. Gli errori di I/O impediscono al PLC di rilevare con precisione le condizioni di campo o di controllare correttamente le apparecchiature.
- Fenomeni comuni: Un punto di ingresso specifico rimane costantemente acceso o spento, senza riflettere lo stato effettivo del sensore; un punto di uscita specifico non riesce ad alimentare il suo carico (ad esempio, elettrovalvola, spia luminosa) oppure il suo stato è anomalo.
- Analisi approfondita delle cause:
- Cablaggio e dispositivi esterni: Malfunzionamento del sensore o dell'attuatore, cablaggio errato (ad esempio mancata corrispondenza NPN/PNP), cortocircuiti o circuiti aperti nel cablaggio sul campo, collegamenti terminali scadenti.
- Hardware del modulo I/O: Guasto di componenti interni come gli optoaccoppiatori, relèo transistor all'interno del modulo; scarso contatto tra il modulo I/O e il backplane.
- Configurazione e programma: Assegnazione errata dell'indirizzo I/O nella configurazione del PLC oppure errori nella logica del programma che impediscono il corretto azionamento del punto I/O corrispondente.
- Strategia efficiente per la risoluzione dei problemi:
- Osservare gli indicatori di stato: La maggior parte dei moduli I/O Omron è dotata di LED di stato per ogni punto, che forniscono un'indicazione iniziale se i segnali stanno raggiungendo il modulo e se il modulo sta tentando di attivare le uscite.
- Utilizzare la funzione "Forza" (utilizzare con cautela): All'interno del software di programmazione (ad esempio, CX-Programmer o Sysmac Studio), utilizzare la funzionalità Forza ON/OFF. Ciò consente di verificare direttamente se un punto di uscita del modulo può pilotare il suo carico o di osservare se lo stato di un punto di ingresso può essere sovrascritto manualmente nel software. Questo aiuta a distinguere tra problemi di campo esterni e problemi interni al modulo/programma. Nota: forzare l'I/O bypassa la logica normale e può causare un comportamento imprevisto della macchina; prestare la massima attenzione.
- Controllare i circuiti esterni: Scollegare il cablaggio di campo dai terminali del modulo. Utilizzare un multimetro, un generatore di segnale o un'apparecchiatura di prova adeguata per verificare direttamente la funzionalità del sensore/attuatore e l'integrità dei cavi di collegamento.
- Scambio di moduli e test incrociati: Sostituire il modulo I/O sospetto con un modulo identico, sicuramente funzionante, da un altro slot o da uno di riserva (si noti che potrebbe essere necessaria una riconfigurazione dell'indirizzo a seconda della serie e della configurazione del PLC). Verificare se il guasto segue il modulo o rimane nello slot/canale.
3. Logica del programma e memoria: garantire la stabilità del core di controllo
Il programma utente è l'intelligenza centrale del PLC e ne detta il comportamento di controllo. Gli errori in questo programma influiscono direttamente sul funzionamento del sistema.
- Fenomeni comuni: L'apparecchiatura funziona in modo contrario alla sequenza logica prevista, il sistema si blocca o genera errori in condizioni specifiche, il download o il caricamento del programma non riesce.
- Analisi approfondita delle cause:
- Errori logici del programma: Logica condizionale incompleta, conflitti di temporizzazione, errori algoritmici, condizioni di gara, cicli infiniti.
- Problemi di gestione dei dati: Overflow di dati, incongruenze tra i tipi di dati durante le operazioni, variabili intermedie critiche sovrascritte involontariamente.
- Problemi di memoria: Danneggiamento delle aree di memoria dei programmi o dei dati (meno comune, ma possibile a causa di forti rumori elettrici, fine del ciclo di vita o shock fisico); esaurimento della batteria con conseguente perdita di dati ritentivi (per PLC che utilizzano RAM con batteria tampone).
- Incompatibilità di versione: Mancata corrispondenza tra la versione del firmware del PLC, la versione del software di programmazione utilizzato o la dipendenza del programma da versioni specifiche dei blocchi funzione.
- Strategia efficiente per la risoluzione dei problemi:
- Monitoraggio e debug online: Sfrutta le funzionalità di monitoraggio online del software di programmazione. Osserva lo stato di esecuzione in tempo reale dei rung ladder o delle sezioni di codice, monitora i valori delle variabili e traccia il flusso logico passo dopo passo. Utilizza i breakpoint per mettere in pausa l'esecuzione in punti specifici e ottenere un'analisi dettagliata.
- Verifica e confronto del programma: Assicurarsi che il programma attualmente in esecuzione nel PLC corrisponda alla versione master salvata sulla workstation di progettazione. Eseguire backup regolari del programma. Utilizzare la funzione di confronto del software, se disponibile.
- Interpretare i codici di errore: Quando il PLC entra in uno stato di errore (indicato dal LED ERROR e da specifici flag/registri), connettersi al software di programmazione per leggere il codice di errore e il messaggio dettagliati. Consultare i manuali di riferimento hardware e di istruzioni Omron per la specifica serie di PLC per comprendere il significato del codice e le azioni consigliate. L'adesione a pratiche di programmazione strutturate, come quelle descritte nella norma IEC 61131-3, può contribuire a ridurre al minimo gli errori logici.
- Controllare lo stato e la diagnostica del PLC: Utilizzare le funzioni diagnostiche all'interno del software di programmazione per verificare lo stato generale del PLC, tra cui lo stato della memoria, la tensione della batteria (se applicabile), il tempo di ciclo e gli errori di sistema.
4. Rete di comunicazione: le arterie dello scambio di informazioni
I moderni sistemi di automazione spesso implicano la comunicazione in rete tra più PLC, HMI (Interfaccia uomo-macchina), VFD, sistemi di visione e altri dispositivi intelligenti.
- Fenomeni comuni: Il PLC non riesce a comunicare con un sistema host (SCADA/HMI) o con altri dispositivi di rete, i dati di comunicazione sono errati o vengono persi in modo intermittente, gli indicatori di stato della rete su moduli/porte si comportano in modo anomalo.
- Analisi approfondita delle cause:
- Collegamento fisico: Cavi di rete (Ethernet) o cavi seriali (RS232/485) danneggiati, connettori allentati, messa a terra della schermatura non corretta, resistori di terminazione mancanti o errati (essenziali per RS485/CAN).
- Configurazione dei parametri: Conflitti di indirizzi IP o incongruenze di subnet (Ethernet), velocità in baud, bit di dati, bit di stop o impostazioni di parità (seriale) errati, numeri di stazione/indirizzi di nodo duplicati, impostazioni errate del protocollo di comunicazione.
- Carico di rete e interferenze: Traffico di rete eccessivo che provoca collisioni o ritardi, interferenze elettromagnetiche (EMI) che corrompono i segnali di comunicazione.
- Errore modulo/porta: Malfunzionamento hardware della porta di comunicazione integrata del PLC o di un modulo di comunicazione aggiuntivo.
- Strategia efficiente per la risoluzione dei problemi:
- Ispezionare le connessioni fisiche e gli indicatori: Verificare l'integrità del cavo e il corretto collegamento a entrambe le estremità. Osservare i LED di collegamento/attività sulle porte/moduli di comunicazione per informazioni sullo stato (ad esempio, collegamento stabilito, trasmissione/ricezione dati in corso).
- Verifica i parametri di comunicazione: Controllare meticolosamente le impostazioni di comunicazione (indirizzo IP, maschera di sottorete, gateway, velocità in baud, parità, indirizzo del nodo, ecc.) su Tutto Dispositivi coinvolti nello specifico collegamento di comunicazione. Garantire la coerenza assoluta.
- Semplifica la rete per i test: Isolare il problema di comunicazione testando le connessioni punto-punto. Scollegare gli altri dispositivi e provare a comunicare solo tra il PLC e un altro dispositivo. Utilizzare strumenti standard come
ping
comando (per reti Ethernet) o software specializzato per test seriali/di rete. - Utilizzare strumenti diagnostici: Le suite software di Omron, come CX-One (che include Network Configurator) o Sysmac Studio, spesso includono strumenti di diagnostica di rete. Questi possono aiutare a visualizzare la rete, identificare i dispositivi connessi, controllare lo stato dei nodi e monitorare il traffico.
- Consultare la documentazione del protocollo: Assicurarsi di avere una conoscenza approfondita del protocollo di comunicazione specifico utilizzato (ad esempio, EtherNet/IP, Modbus TCP, RS485 Modbus RTU, FINS di Omron). Fare riferimento ai manuali e alle specifiche del protocollo Omron per dettagli su struttura, tempistica e gestione degli errori dei messaggi.
5. Altri problemi comuni e soluzioni
Categoria di guasto | Possibili cause | Suggerimenti rapidi per la risoluzione dei problemi | Misure preventive |
---|---|---|---|
Guasto del modulo di espansione | Guasto hardware del modulo, scarsa connessione del backplane, mancata corrispondenza della configurazione (tabella I/O), problema con il cavo del bus | Controllare gli indicatori del modulo, riposizionare saldamente il modulo, verificare i collegamenti dei cavi del bus, ricontrollare la configurazione della tabella I/O nel software | Pulisci periodicamente gli slot, assicurati un montaggio sicuro, esegui il backup della configurazione |
Sovratemperatura | La temperatura ambiente supera le specifiche, scarsa ventilazione/flusso d'aria, accumulo di polvere, carico eccessivo della CPU/modulo | Misurare la temperatura ambiente, pulire ventole e prese d'aria, controllare la percentuale di carico del PLC (tempo di ciclo) | Assicurare un adeguato raffreddamento/ventilazione del pannello di controllo, evitare la luce solare diretta, eseguire una pulizia regolare |
Software/Compatibilità | Versione del software di programmazione incompatibile, driver mancanti, conflitti del sistema operativo sul PC di programmazione | Aggiornare software/firmware a versioni compatibili, installare driver corretti, verificare i requisiti ambientali del PC | Utilizzare versioni software ufficialmente consigliate, mantenere il sistema operativo aggiornato, documentare le configurazioni software/hardware |
Modulo di funzione speciale | Guasto hardware del modulo, impostazioni dei parametri errate (ad esempio, contatore ad alta velocità, uscita a impulsi) | Eseguire il test con un modulo di riserva, rivedere meticolosamente il manuale del modulo e le impostazioni dei parametri, utilizzare la diagnostica software per il modulo | Comprendere appieno le capacità del modulo e le definizioni dei parametri, seguire attentamente le istruzioni del manuale |
Rischi di aggiornamento del sistema | Incompatibilità firmware/programma dopo l'aggiornamento, danneggiamento dei dati dovuto all'interruzione dell'aggiornamento | Fondamentale: eseguire il backup del programma e dei dati prima dell'aggiornamento, leggere attentamente le note di rilascio, garantire alimentazione e comunicazione stabili durante l'aggiornamento | Scegli le finestre di aggiornamento appropriate, in caso di dubbi, rivolgiti al supporto tecnico Omron |
Prospettiva di analisi dei dati: incidenza dei guasti e impatto dei tempi di inattività (esempio illustrativo)
Sebbene i dati precisi varino significativamente in base alle specifiche dell'applicazione e alle pratiche di manutenzione, l'esperienza del settore suggerisce alcune tendenze nella distribuzione dei tipi di guasto. La tabella seguente fornisce dati illustrativi solo a scopo di riferimento:
Tipo di errore | Frequenza relativa stimata | Impatto medio dei tempi di inattività (non preparato) | Impatto medio dei tempi di inattività (diagnosi preparata/competente) |
---|---|---|---|
Guasto all'alimentatore | Medio | Alto (arresto totale del sistema) | Medio (richiede un pezzo di ricambio) |
Errore I/O | Alto | Medio (errore di funzione locale) | Basso (identificazione rapida dei punti e riparazione/sostituzione) |
Errore logico del programma | Medio-Alto | Da medio ad alto (comportamento irregolare/arresto) | Medio (dipendente dall'abilità di debug) |
Errore di comunicazione | Medio-Alto | Da medio ad alto (errore di collegamento del sistema) | Medio (controllo parametri/test collegamento) |
Guasto del modulo hardware | Da basso a medio | Medio (richiede un pezzo di ricambio) | Da basso a medio (sostituzione di pezzi di ricambio) |
Ambientale/Altro | Basso | Da basso a medio | Basso (Migliora l'ambiente/Standardizza le operazioni) |
Nota: questa tabella è concettuale e non rappresenta dati statistici precisi.
Conclusione:
I PLC Omron sono componenti fondamentali per un'automazione industriale efficiente e affidabile. In caso di potenziali guasti, è fondamentale adottare una metodologia diagnostica sistematica e basata sull'evidenza.
Dai controlli fondamentali degli alimentatori e dei cablaggi I/O alle analisi complesse della logica del programma e delle reti di comunicazione, ogni passaggio richiede pazienza e attenzione meticolosa.
La comprensione dei sintomi tipici e delle cause profonde dei vari guasti, l'acquisizione di competenze nell'uso del software di programmazione e delle utilità diagnostiche di Omron e l'applicazione delle strategie descritte in questa guida, unitamente alla prospettiva dei dati, consentiranno a ingegneri e tecnici di migliorare significativamente l'efficienza nella risoluzione dei problemi.
È fondamentale che l'adozione di solide pratiche di manutenzione preventiva, come ispezioni regolari, pulizie, backup dei programmi e monitoraggio dell'ambiente operativo, possa ridurre al minimo in modo proattivo il verificarsi di guasti.
Questo approccio garantisce le massime prestazioni e longevità dei sistemi PLC Omron, salvaguardando la stabilità della produzione e ottenendo in definitiva una riduzione dei costi e un miglioramento dell'efficienza.
Per problemi particolarmente complessi o persistenti, si consiglia sempre di consultare la documentazione ufficiale Omron o di contattare l'assistenza tecnica Omron.
Dai potenza ai tuoi progetti con i nuovi PLC originali Omron, Mitsubishi e Schneider, disponibili in magazzino e pronti da subito!
Contattaci
Basta compilare il tuo nome, indirizzo email e una breve descrizione della tua richiesta in questo modulo. Ti contatteremo entro 24 ore.
Categoria di prodotto
Prodotti in saldo
Potresti trovare interessanti anche questi argomenti
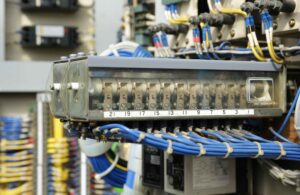
Le 10 principali caratteristiche dei PLC Omron che li rendono leader del settore
I controllori logici programmabili (PLC) sono la spina dorsale dell'automazione industriale moderna e Omron è sempre stata all'avanguardia in questa tecnologia. I PLC Omron sono rinomati per la loro affidabilità, versatilità e funzionalità avanzate, il che li rende la scelta migliore per le industrie di tutto il mondo. In questo articolo, esploreremo le 10 principali funzionalità dei PLC Omron che li distinguono come leader del settore.
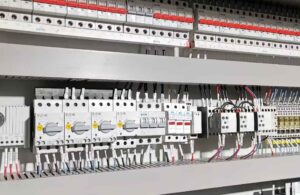
Sensore di prossimità vs sensore fotoelettrico
Questo articolo si addentra nell'affascinante regno dei sensori di prossimità e dei sensori fotoelettrici, esplorandone funzionalità, differenze e applicazioni. Che tu sia un ingegnere esperto in una fabbrica di macchinari e attrezzature o un fornitore di soluzioni alla ricerca dei migliori componenti di automazione, comprendere questi tipi di sensori è fondamentale. Come stabilimento di produzione di prodotti di controllo e automazione industriale, siamo qui per illuminare le complessità di questi componenti vitali, guidandoti infine verso decisioni informate per i tuoi progetti.
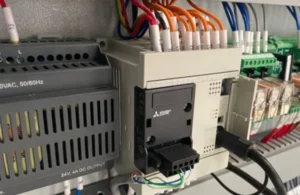
I 7 marchi PLC più popolari
I 7 marchi di PLC più popolari Scegliere il marchio di PLC giusto tra le numerose opzioni disponibili può essere difficile. Non