Tot ce trebuie să știți despre contactori și cum funcționează aceștia
Cuprins
Ce este un contactor și pentru ce este folosit?
Un contactor este un comutator controlat electric utilizat pentru comutarea unui circuit electric, similar unui releu. Cu toate acestea, spre deosebire de un releu, un contactor este utilizat în aplicații cu capacitate de purtare a curentului mai mare.
Fiind o persoană profund implicată în automatizarea industrială și produsele de control industrial, am văzut direct cum contactorii joacă un rol esențial în gestionarea circuitelor de mare putere. Acestea sunt proiectate pentru a fi conectate direct la dispozitive de sarcină cu curent ridicat.
Când este alimentată, bobina din interiorul contactorului creează un câmp magnetic, care face ca miezul contactorului să se miște și să închidă contactele, permițând curentului să circule către sarcină.
Contactoarele sunt utilizate cel mai frecvent cu motoarele electrice și sunt proiectate și construite pentru a face față sarcinilor grele și comutărilor frecvente pe care aceste aplicații le necesită.
De exemplu, în fabricile noastre de producție, folosim contactori pentru a controla motoare mari care alimentează benzile noastre transportoare și alte mașini grele. Capacitatea lor de a gestiona cantități mari de energie electrică le face o componentă esențială a sistemelor noastre electrice. Un contactor este utilizat pentru a controla puterea motoarelor, iluminatului, încălzirii și a altor sarcini electrice.
Care sunt diferitele tipuri de contactori?
Sunt disponibile diverse tipuri de contactori, fiecare proiectat pentru aplicații specifice. Unele tipuri comune includ contactoare AC și contactoare DC, contactoare cu scop precis, contactoare monofazate și trifazate.
Fiecare tip de contactor are propriul set de caracteristici și este utilizat în diferite scenarii în funcție de cerințele circuitului electric și de sarcina pe care o controlează. Îmi amintesc un caz în care a trebuit să trecem de la un contactor de curent alternativ la un contactor de curent continuu când ne-am modernizat sistemul de alimentare cu energie, ceea ce a îmbunătățit semnificativ eficiența controlului motorului nostru.
Tip de contactor | Descriere | Aplicații tipice |
---|---|---|
Contactor AC | Proiectat pentru utilizare în circuite de curent alternativ, optimizat pentru comutarea sarcinilor de curent alternativ. | Motoare, iluminat, sisteme de incalzire in retelele de curent alternativ. |
Contactor DC | Proiectat pentru utilizare în circuite DC, optimizat pentru comutarea sarcinilor DC. | Sisteme de baterii, motoare DC, sisteme de energie regenerabilă. |
Contactor cu scop definit | Adaptat pentru aplicații specifice precum aer condiționat, refrigerare. | Sisteme HVAC, unități frigorifice. |
Contactor de iluminat | Utilizat special pentru comutarea sarcinilor de iluminat. | Iluminat industrial si comercial. |
Releu | Un tip de releu care comută sarcini mai mici. | Circuite de control, sisteme de automatizare. |
Contactor monofazat | Destinat sistemelor de alimentare monofazate, de obicei cu capacități de tensiune și curent mai mici în comparație cu contactoarele trifazate. | Aplicații rezidențiale și comerciale ușoare. |
Contactor trifazat | Proiectat pentru sisteme de alimentare trifazate, capabile să suporte tensiuni și curent mai mari. | Mașini industriale, motoare mari. |
Cum funcționează un contactor? Principiul de funcționare
Principiul de funcționare al unui contactor implică o bobină electromagnetică și un set de contacte. Când curentul electric trece prin bobină, acesta generează un câmp magnetic care atrage un miez mobil, numit și armătură.
Această mișcare face ca contactele să se închidă, permițând curentului să circule prin circuit către sarcină. Când bobina este dezactivată, câmpul magnetic dispare, iar un arc readuce contactele în poziția lor normal deschisă, întrerupând fluxul de curent.
În cazurile noastre de inginerie, folosim contactori pentru a controla motoare mari. Când butonul de pornire este apăsat, bobina contactorului este alimentată, creând un câmp magnetic care închide contactele și pornește motorul.
Când butonul de oprire este apăsat, bobina este scoasă din sub tensiune, iar contactele se deschid, oprind motorul. Acest proces permite operarea sigură și eficientă de la distanță a dispozitivelor de mare putere.
Care este diferența dintre contactori și relee?
În timp ce atât contactorii, cât și releele sunt folosite pentru a comuta circuitele electrice, există diferențe cheie între ele. Contactoarele sunt proiectate să suporte curenți și tensiuni mult mai mari decât releele.
Ele sunt utilizate de obicei în aplicații în care motoarele mari sau alte dispozitive de mare putere trebuie controlate. Releele sunt utilizate în general pentru aplicații și semnalizare cu putere redusă. În plus, contactoarele au adesea caracteristici precum suprimarea arcului pentru a gestiona curenții mari și a preveni deteriorarea. Un mare exemplu în acest sens este în nostru HMI Mitsubishi.
Caracteristică | Contactor | Releu |
---|---|---|
Evaluare curentă | Ridicat (de obicei peste 10A) | Scăzut (de obicei sub 10A) |
Tensiune nominală | Ridicat (până la 1000 V sau mai mult) | Scăzut spre mediu (până la 250V) |
Dimensiune | Mai mare | Mai mic |
Aplicații | Motoare, utilaje grele, control industrial, iluminat | Comutarea semnalului, circuite de control, aplicații de putere redusă |
Suprimarea arcului | Echipat adesea cu jgheaburi de arc sau alte mecanisme de suprimare a arcului | De obicei, nu este echipat cu suprimarea arcului |
Contacte | De obicei deschis (NO), poate avea mai mulți poli | Poate fi NO, NC (normal închis) sau comutator (CO) |
Durabilitate | Proiectat pentru comutare frecventă la sarcini mari | Proiectat pentru comutare mai puțin frecventă la sarcini mai ușoare |
Tensiunea bobinei | Tensiuni standardizate ale bobinei (de exemplu, 24V, 120V, 230V, 480V) | Gamă largă de tensiuni de bobină, inclusiv tensiuni joase (de exemplu, 5V) |
Cost | Mai mare datorită construcției robuste și capacității mai mari | Mai scăzut datorită construcției mai simple și capacității mai mici |
Zgomot | Poate produce zgomot audibil în timpul funcționării datorită pieselor mobile mai mari | Funcționare în general mai silențioasă |
În operațiunile noastre, folosim relee pentru semnale de control și contactoare pentru comutarea puterii. De exemplu, un releu poate fi folosit pentru a activa un senzor, în timp ce un contactor este folosit pentru a porni un motor mare pe baza intrării senzorului respectiv. Această diviziune a muncii asigură fiabilitatea și siguranța sistemelor noastre electrice.
Cum să selectați contactorul potrivit: un ghid de selecție a contactorilor
Selectarea contactorului potrivit pentru aplicația dvs. este crucială pentru a asigura funcționarea corectă și longevitatea echipamentului dumneavoastră. Factorii de luat în considerare includ tensiunea și curentul nominal, tipul de sarcină (de exemplu, motor, iluminat, încălzire), numărul de poli și mediul de operare.
Asigurați-vă că contactorul poate gestiona tensiunea și curentul maxim de funcționare ale circuitului. De asemenea, este important să luați în considerare ciclul de funcționare și numărul așteptat de operațiuni de comutare.
Când proiectam o nouă linie de producție, a trebuit să selectăm cu atenție contactori care să poată face față curenților mari de pornire ai motoarelor noastre.
Am consultat specificațiile producătorului și am ales contactori cu valori nominale și caracteristici electrice adecvate, cum ar fi contacte auxiliare pentru circuitele de comandă.
Contactor AC vs. Contactor DC: De care aveți nevoie?
Contactoarele AC sunt proiectate pentru utilizarea în circuite de curent alternativ, în timp ce contactoarele DC sunt proiectate pentru circuite de curent continuu. Principala diferență constă în modul în care gestionează arcul care este generat atunci când contactele se deschid și se închid.
Contactoarele AC folosesc trecerea prin zero a formei de undă AC pentru a ajuta la stingerea arcului, în timp ce contactoarele DC necesită mecanisme suplimentare de suprimare a arcului.
În cazurile noastre de inginerie, folosim contactori AC pentru majoritatea echipamentelor noastre, deoarece sursa noastră de alimentare este AC.
Cu toate acestea, avem unele echipamente specializate care folosesc curent continuu, iar pentru acestea, folosim contactoare CC cu jgheaburi pentru arc pentru a gestiona arcul. Puteți găsi multe PLC Mitsubishi tipurile sunt vândute online pe site-ul nostru.
Înțelegerea diagramelor de cablare a contactorului
O diagramă de cablare a contactorului arată modul în care contactorul este conectat într-un circuit electric. Acesta include de obicei bobina, contactele principale și orice contact auxiliar. Înțelegerea acestor diagrame este esențială pentru instalarea și depanarea corectă a contactoarelor.
Aceste cunoștințe au fost de neprețuit în diagnosticarea și remedierea rapidă a problemelor cu echipamentele noastre. Omron HMI dispozitivele oferă diagrame detaliate care au ajutat enorm echipa noastră.
Evaluări electrice și specificații ale contactoarelor
Contactoarele au diferite valori electrice care specifică limitele lor de funcționare. Acestea includ tensiunea nominală, curentul nominal, capacitatea de comutare și rezistența mecanică și electrică.
Este esențial să selectați un contactor cu valori nominale care îndeplinesc sau depășesc cerințele aplicației dumneavoastră. Puteți găsi informații detaliate despre evaluările electrice în site-ul nostru Proface HMI manuale.
De exemplu, când am instalat motoare noi în fabrica noastră, a trebuit să ne asigurăm că contactorul pe care l-am selectat avea un curent nominal mai mare decât curentul la sarcină maximă al motorului pentru a gestiona curenții de pornire în timpul pornirii. Am luat în considerare și temperatura ambiantă și am ales contactori cu factori de derating corespunzători.
Aplicații ale contactorelor în automatizarea industrială
Contactoarele sunt utilizate pe scară largă în automatizarea industrială pentru controlul motoarelor, sistemelor de iluminat, elementelor de încălzire și a altor dispozitive de mare putere.
Ele fac parte integrantă din pornitoarele de motoare, panourile de control și alte echipamente de automatizare. Capacitatea lor de a face față curenților mari și comutările frecvente le face ideale pentru aceste aplicații.
Folosim contactori în diverse aplicații, de la controlul motoarelor de pe benzile noastre transportoare până la gestionarea iluminatului în zonele noastre de producție. Fiabilitatea și durabilitatea lor sunt esențiale pentru menținerea eficienței producției noastre.
Întreținerea și depanarea contactoarelor
Întreținerea regulată a contactoarelor este importantă pentru a asigura funcționarea corectă a acestora și pentru a preveni defecțiunile. Aceasta include inspectarea contactelor pentru uzură și deteriorare, verificarea rezistenței bobinei și asigurarea că contactorul este montat și cablat corespunzător.
Depanarea problemelor obișnuite cu contactoarele implică verificarea conexiunilor slăbite, bobine arse și contacte uzate sau deteriorate. Din experiența noastră, inspecțiile regulate și înlocuirea la timp a componentelor uzate ne-au ajutat să minimizăm timpul de nefuncționare și să ne menținem producția să funcționeze fără probleme.
Întrebări frecvente
Un contactor este un comutator controlat electric utilizat pentru comutarea unui circuit electric. Este conceput pentru a gestiona curenți mari și este utilizat în mod obișnuit pentru a controla motoare, iluminat și alte dispozitive de mare putere în aplicații industriale.
În timp ce atât contactoarele, cât și releele comută circuitele electrice, contactoarele sunt proiectate pentru aplicații de înaltă tensiune și curent, în timp ce releele sunt utilizate pentru aplicații cu putere mai mică. Contactoarele includ adesea caracteristici de suprimare a arcului.
Când selectați un contactor, luați în considerare valorile nominale de tensiune și curent, tipul de sarcină, numărul de poli, mediul de funcționare și ciclul de funcționare. Asigurați-vă că contactorul poate gestiona tensiunea și curentul maxim de funcționare ale circuitului.
Principalele tipuri de contactoare includ contactoare AC, contactoare DC, contactoare cu scop precis, contactoare monofazate și trifazate. Fiecare tip este proiectat pentru aplicații și condiții de operare specifice.
Întreținerea regulată a contactoarelor include inspectarea contactelor pentru uzură și deteriorare, verificarea rezistenței bobinei și asigurarea că contactorul este montat și cablat corespunzător.
Alimentați-vă proiectele cu PLC Omron, Mitsubishi, Schneider nou-nouț, original – în stoc, gata acum!
Concluzie
- Contactoarele sunt componente esențiale în automatizarea industrială, utilizate pentru comutarea circuitelor electrice de mare curent.
- Există diferite tipuri de contactori, inclusiv contactori AC și DC, fiecare proiectat pentru aplicații specifice.
- Principiul de funcționare al unui contactor implică o bobină electromagnetică și un set de contacte care se închid atunci când bobina este alimentată.
- Contactoarele diferă de relee prin capacitatea lor de a gestiona curenți și tensiuni mai mari.
- Selectarea contactorului potrivit necesită luarea în considerare a unor factori precum tensiunea și curentul nominal, tipul de sarcină și mediul de operare.
- Întreținerea regulată și depanarea sunt cruciale pentru a asigura fiabilitatea și longevitatea contactoarelor.
Înțelegând informațiile prezentate în acest ghid, puteți lua decizii informate cu privire la selectarea, utilizarea și întreținerea contactorilor în sistemele dumneavoastră de automatizare industrială. Pentru întrebări suplimentare sau pentru a discuta nevoile dumneavoastră specifice, vă rugăm Contact S.U.A. Echipa noastră de experți este pregătită să vă asiste în optimizarea proceselor dumneavoastră de control industrial.
Contactaţi-ne
Doar completați numele dvs., adresa de e-mail și o scurtă descriere a solicitării dvs. în acest formular. Vă vom contacta în termen de 24 de ore.
Categoria de produs
Produse de vânzare fierbinte
De asemenea, puteți găsi aceste subiecte interesante
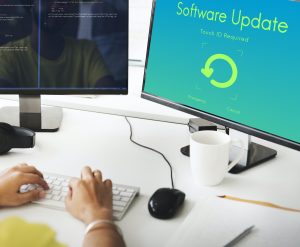
Cum să descărcați și să încărcați programe pentru seria Hitech (Beijer) HMI PWS6000: un ghid cuprinzător
Cum să descărcați și să încărcați programe pentru seria Hitech (Beijer) HMI PWS6000: un ghid cuprinzător Seria Hitech (Beijer) PWS6000
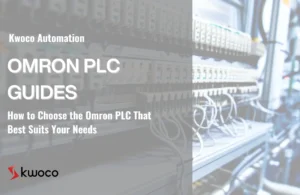
Cum să alegeți PLC-ul Omron care se potrivește cel mai bine nevoilor dvs
Cum să alegeți PLC-ul Omron care se potrivește cel mai bine nevoilor dvs. Luptați pentru a găsi PLC-ul potrivit pentru industria dvs.
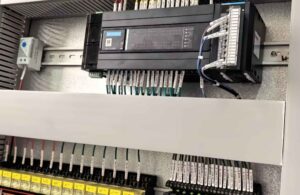
Precizie de deblocare: stăpânirea codificatoarelor și a contoarelor de mare viteză cu PLC-uri
Acest articol se scufundă adânc în lumea codificatoarelor și a contoarelor de mare viteză (HSC), explicând modul în care acestea se interacționează cu controlerele logice programabile (PLC) pentru a oferi un control precis în aplicațiile de automatizare industrială. De la înțelegerea codificatoarelor rotative până la configurarea modulelor HSC, vom explora modul în care aceste tehnologii funcționează împreună pentru a îmbunătăți controlul vitezei, măsurarea poziției și eficiența generală a sistemului.