Apa itu PLC Keamanan? Memahami Keamanan dan Otomasi
PLC Keamanan adalah jenis khusus Sistem Pemrosesan Akhir (PLC) dirancang untuk mengelola dan memantau fungsi-fungsi yang berkaitan dengan keselamatan dalam sistem otomasi. Tidak seperti PLC standar, PLC keselamatan dibuat untuk mematuhi standar keselamatan yang ketat, memastikan bahwa setiap potensi bahaya dikurangi secara efektif.
Daftar isi
Apa itu PLC Keamanan?
PLC Keamanan dirancang khusus untuk menangani tugas-tugas yang berkaitan dengan keselamatan dalam lingkungan industri. Perangkat ini dirancang untuk memastikan bahwa mesin beroperasi dengan aman dan dapat diprediksi, sehingga mengurangi risiko kecelakaan.
Arsitektur PLC keselamatan mencakup komponen-komponen redundan untuk meningkatkan keandalan dan meminimalkan kemungkinan kegagalan.
Fitur Utama PLC Keamanan
- Fungsi Keamanan Terpadu: PLC Keamanan dilengkapi dengan fitur yang memantau operasi penting terkait keselamatan. PLC dapat mendeteksi kesalahan dan anomali, memastikan bahwa sistem merespons dengan tepat.
- Kepatuhan terhadap Standar Keselamatan: PLC Keamanan harus mematuhi standar keselamatan internasional seperti IEC 61508, yang mendefinisikan keselamatan fungsional sistem terkait keselamatan listrik/elektronik/elektronik yang dapat diprogram.
- Kontrol Aliran Program: Kontrol aliran program yang efektif dalam PLC keselamatan menjamin bahwa fungsi keselamatan dijalankan dengan cara yang aman dan dapat diprediksi.
Aplikasi PLC Keamanan
PLC Keamanan digunakan dalam berbagai aplikasi, termasuk:
- Keamanan Mesin: Mereka mengendalikan perangkat keselamatan seperti tirai cahaya dan kunci pengaman untuk melindungi pekerja.
- Otomatisasi Proses: Di lingkungan berbahaya, PLC keselamatan memastikan bahwa proses diotomatisasi dengan tetap menjaga keselamatan.
Apa yang membedakan PLC Keselamatan dengan PLC Standar?
Meskipun kedua jenis PLC tersebut memainkan peran penting dalam otomasi, PLC keselamatan dan PLC standar memiliki fungsi yang berbeda. PLC standar terutama digunakan untuk tugas kontrol umum, sedangkan PLC keselamatan berfokus pada operasi pengamanan.
Perbedaan Dijelaskan
- Fungsionalitas: PLC standar mengelola tugas operasional rutin tanpa pertimbangan keselamatan, sedangkan PLC keselamatan mengintegrasikan fungsi keselamatan ke dalam pemrogramannya.
- Tingkat Integritas Keselamatan (SIL): PLC keselamatan harus memenuhi persyaratan SIL tertentu, yang tidak dimiliki oleh PLC standar. Hal ini membuat PLC keselamatan lebih andal dalam situasi berbahaya.
- Kompleksitas Pemrograman: Pemrograman PLC keselamatan sering kali melibatkan langkah-langkah dan protokol keselamatan tambahan, sehingga membuatnya lebih rumit dibandingkan dengan pemrograman PLC standar.
Memilih PLC yang Tepat
Saat memutuskan antara PLC keselamatan dan PLC standar, pertimbangkan hal berikut:
- Persyaratan KeselamatanJika aplikasi Anda melibatkan lingkungan berbahaya, pilihlah PLC yang aman.
- Kepatuhan terhadap PeraturanPastikan kepatuhan terhadap standar keselamatan yang relevan dengan industri Anda.
Apa Fungsi Keselamatan utama dari PLC Keselamatan?
Fungsi keselamatan sangat penting untuk pengoperasian PLC keselamatan. Fungsi-fungsi ini dirancang untuk mendeteksi kesalahan dan memastikan bahwa mesin beroperasi dengan aman.
Fungsi Keselamatan Umum
- Pemberhentian Darurat: Fungsi keselamatan mendasar yang menghentikan operasi segera untuk mencegah kecelakaan.
- Torsi Aman Mati (STO): Fungsi ini memutus daya ke motor, mencegahnya menghasilkan torsi, yang sangat penting dalam menghentikan mesin secara efektif.
- Pemantauan Keamanan: Pemantauan berkelanjutan terhadap operasi terkait keselamatan memastikan bahwa setiap anomali terdeteksi dan ditangani dengan segera.
Implementasi Fungsi Keselamatan
Mengintegrasikan fungsi keselamatan memerlukan:
- Pemrograman yang cermat: Pemrograman PLC harus memperhitungkan semua kemungkinan mode kegagalan.
- Pengujian Reguler: Fungsi keselamatan harus menjalani pengujian rutin untuk memastikannya beroperasi dengan benar dalam semua kondisi.
Memahami Tingkat Integritas Keselamatan (SIL)
Safety Integrity Level (SIL) adalah ukuran keandalan fungsi keselamatan dalam suatu sistem keselamatan. SIL berkisar dari SIL 1 (terendah) hingga SIL 4 (tertinggi), yang menunjukkan kemungkinan bahwa suatu fungsi keselamatan akan berfungsi dengan benar dalam menanggapi suatu kejadian berbahaya.
Pentingnya SIL
Memahami SIL penting untuk:
- Penilaian Risiko: Mengidentifikasi tindakan keselamatan yang diperlukan tergantung pada risiko yang terkait dengan suatu proses.
- Memilih PLC Keamanan: Memastikan bahwa PLC keselamatan yang dipilih memenuhi SIL yang diperlukan untuk aplikasi Anda.
Kepatuhan terhadap IEC 61508
IEC 61508 mendefinisikan persyaratan untuk mencapai berbagai tingkat SIL, yang memandu desain dan implementasi sistem keselamatan. Kepatuhan terhadap standar ini memastikan bahwa PLC keselamatan kuat dan andal.
Mengapa PLC Keselamatan Penting untuk Keselamatan di Tempat Kerja?
Integrasi PLC keselamatan dalam lingkungan industri secara signifikan meningkatkan keselamatan di tempat kerja. PLC menyediakan pendekatan sistematis untuk mengelola risiko yang terkait dengan mesin dan proses otomasi.
Meningkatkan Keselamatan di Tempat Kerja
- Pencegahan Kecelakaan: Dengan mengendalikan fungsi keselamatan, PLC keselamatan membantu mencegah kecelakaan yang dapat mengakibatkan cedera atau kematian.
- Peningkatan Produktivitas:Lingkungan kerja yang lebih aman akan meningkatkan moral dan produktivitas karyawan karena pekerja merasa aman di lingkungannya.
Kepatuhan terhadap Peraturan
Banyak industri yang tunduk pada standar dan peraturan keselamatan yang ketat. Menerapkan PLC keselamatan tidak hanya memastikan kepatuhan tetapi juga menunjukkan komitmen terhadap keselamatan di tempat kerja.
Pertanyaan yang Sering Diajukan
PLC Keselamatan dirancang untuk menangani fungsi keselamatan dan mematuhi standar keselamatan yang ketat, sedangkan PLC standar digunakan untuk tugas kontrol umum.
PLC Keselamatan umumnya digunakan dalam keselamatan mesin, otomatisasi proses, dan aplikasi apa pun yang mengutamakan keselamatan.
Tingkat SIL membantu menentukan keandalan fungsi keselamatan dan memandu pemilihan PLC keselamatan berdasarkan risiko yang terkait dengan berbagai proses.
Pengujian rutin memastikan bahwa fungsi keselamatan beroperasi dengan benar dan dapat mendeteksi serta mengurangi bahaya secara efektif.
Standar keselamatan menyediakan pedoman untuk desain, implementasi, dan pengoperasian PLC keselamatan, memastikan kepatuhan dan keandalan.
Dukung proyek Anda dengan PLC Omron, Mitsubishi, Schneider baru dan asli – tersedia sekarang!
Kesimpulan
Singkatnya, PLC keselamatan merupakan komponen penting dalam sistem otomasi modern, yang memastikan bahwa keselamatan di tempat kerja menjadi prioritas. Berikut adalah poin-poin penting yang perlu diingat:
- PLC Keamanan dirancang untuk aplikasi kritis terhadap keselamatan.
- Mereka berbeda secara signifikan dari PLC standar dalam hal fungsionalitas dan kepatuhan terhadap standar keselamatan.
- Memahami Tingkat Integritas Keselamatan (SIL) sangat penting untuk memilih PLC keselamatan yang tepat.
- Pengujian dan pemantauan fungsi keselamatan secara berkala diperlukan untuk menjaga lingkungan kerja yang aman.
Sedang mencari PLC baru dan asli untuk proyek Anda? Di Kwoco, kami menyediakan PLC terbaru dari merek-merek ternama seperti Omron, Mitsubishi, Dan Bahasa Inggris SchneiderBerbelanja dengan percaya diri—pengiriman cepat, kualitas terjamin! Beli Sekarang
Hubungi kami
Cukup isi nama, alamat email, dan deskripsi singkat pertanyaan Anda dalam formulir ini. Kami akan menghubungi Anda dalam waktu 24 jam.
Kategori Produk
Produk Penjualan Panas
Anda Mungkin Juga Menemukan Topik Ini Menarik
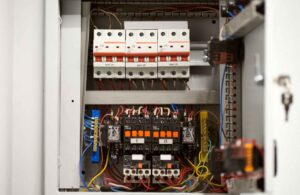
Apa itu Panel Kontrol Listrik? Penjelasan Penting
Panel kontrol listrik merupakan komponen penting dalam otomasi industri, yang berfungsi sebagai pusat kendali dan pemantauan berbagai perangkat listrik. Artikel ini membahas dasar-dasar panel kontrol listrik, komponen-komponennya, dan signifikansinya dalam memastikan operasi yang efisien dan aman dalam lingkungan industri.
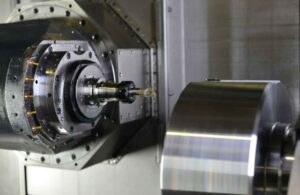
Menguraikan Perbedaan Antara Motor Servo dan Motor Spindel dalam Aplikasi CNC
Artikel ini membahas secara mendalam perbedaan antara motor servo dan motor spindel, dua komponen penting dalam dunia permesinan CNC. Memahami perbedaan ini sangat penting bagi siapa pun yang terlibat dalam otomasi industri, mulai dari teknisi berpengalaman hingga mereka yang baru mengenal bidang ini. Kami akan membahas karakteristik, aplikasi, dan kontribusi uniknya terhadap presisi dan efisiensi mesin CNC.
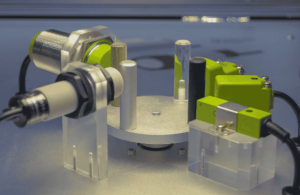
Sensor Kedekatan Induktif 3-Kabel: Panduan Lengkap
Apakah Anda ingin memahami cara kerja sensor jarak induktif 3-kawat dalam otomasi industri? Perangkat penginderaan penting ini telah merevolusi proses manufaktur modern dengan menyediakan deteksi objek logam yang andal dan tanpa kontak.