Ethernet vs Modbus: Mana yang Paling Menopang Pabrik Anda?
Ethernet telah menjadi protokol komunikasi standar untuk jaringan pabrik. Sementara itu, Modbus masih banyak digunakan dalam sistem otomasi proses dan SCADA. Memahami perbedaannya sangat penting untuk membuat pilihan yang tepat bagi proyek Anda.
Daftar isi
Apa itu Ethernet?
Ethernet adalah protokol jaringan yang utamanya digunakan untuk membangun Jaringan Area Lokal (LAN) dan Jaringan Area Luas (WAN). Ethernet distandarkan oleh IEEE sebagai 802.3 pada tahun 1983 dan sejak saat itu telah menjadi salah satu teknologi komunikasi yang paling banyak diadopsi di seluruh dunia.
Fitur dan Fungsi Utama Ethernet
- Kecepatan Transmisi Tinggi: Ethernet mendukung kecepatan dari 10 Mbps hingga 1 Gbps, dengan versi modern mencapai hingga 10 Gbps (10GbE), menjadikannya ideal untuk lingkungan permintaan data tinggi seperti pusat data dan komputasi awan.
- Standar Terbuka: Ethernet terintegrasi secara mulus dengan protokol TCP/IP, menjadikannya pilihan yang sangat baik untuk menghubungkan sistem TI dan otomasi industri.
- Dukungan untuk Berbagai Topologi: Ethernet memungkinkan konfigurasi bintang, cincin, dan bus, membuatnya fleksibel untuk lingkungan jaringan dan perangkat yang berbeda.
- Penerapan dan Perluasan yang Mudah: Ethernet menggunakan kabel umum seperti Cat5e, Cat6, dan serat optik, sehingga menyederhanakan pemasangan dan mengurangi biaya. Ethernet juga mendukung koneksi nirkabel untuk perluasan jaringan yang lebih mudah.
Berkat fitur-fitur ini, Ethernet telah menjadi penting dalam jaringan industri dan komersial, terutama dalam lingkungan data-intensif.
Mengapa Ethernet Populer di Lingkungan Industri?
Ethernet Industri, seperti EtherNet/IP, memperluas Ethernet tradisional dengan kemampuan transmisi data dan sinkronisasi secara real-time. Hal ini penting untuk aplikasi yang memerlukan kontrol dan pemantauan yang presisi, seperti kontrol gerakan dan sinkronisasi proses.
EtherNet/IP memanfaatkan Common Industrial Protocol (CIP) untuk memastikan komunikasi yang lancar di seluruh perangkat dari berbagai vendor, sehingga mengurangi biaya dan kompleksitas integrasi. Selain itu, bandwidth dan fleksibilitas Ethernet yang tinggi membuatnya cocok untuk aplikasi Industrial IoT (IIoT), yang mendukung pemantauan data secara real-time dan integrasi yang lancar dengan sistem TI.
Dengan kemajuan seperti Time-Sensitive Networking (TSN), Ethernet kini dapat memberikan komunikasi deterministik dan latensi rendah, yang memastikan stabilitas dan keandalan sistem untuk operasi kritis. Hasilnya, Ethernet industri memainkan peran penting dalam memodernisasi pabrik untuk efisiensi yang lebih tinggi dan operasi yang lebih cerdas.
Apa itu Modbus?
Modbus adalah protokol pengiriman pesan yang dikembangkan oleh Modicon pada tahun 1979 untuk memfasilitasi komunikasi antara Programmable Logic Controller (PLC (Sistem Kontrol PLC)) dan perangkat lainnya. Dikenal karena kesederhanaan dan kompatibilitasnya, Modbus tetap menjadi protokol andalan untuk otomasi industri.
Keuntungan Utama Modbus
- Mendukung Berbagai Media Komunikasi: Modbus dapat mengirimkan data melalui RS-232, RS-485, dan Ethernet, membuatnya serbaguna untuk berbagai aplikasi.
- Sederhana dan Mudah Digunakan:Model komunikasi master-slave memastikan penerapan yang mudah, membuatnya ideal untuk sistem kontrol skala kecil.
- Protokol Terbuka: Sebagai standar terbuka, Modbus memungkinkan perangkat dari berbagai produsen untuk berkomunikasi dengan lancar, memperluas pilihan peralatan dan mengurangi biaya integrasi sistem.
Karena keandalannya, Modbus tetap menjadi standar dalam sistem SCADA untuk otomatisasi dan pemantauan proses. Sifatnya yang terbuka membuatnya diterima secara luas dan mudah diintegrasikan ke dalam infrastruktur Ethernet modern melalui Modbus TCP/IP.
Kasus Penggunaan Umum untuk Modbus
Modbus sering digunakan dalam sistem SCADA untuk memantau dan mengumpulkan data dalam proses industri. Modbus menyediakan bahasa umum bagi perangkat untuk mengomunikasikan informasi penting, seperti pengukuran suhu dan kelembapan, kembali ke pengontrol pusat.
Fleksibilitasnya membuat Modbus cocok tidak hanya untuk otomasi industri tetapi juga untuk pemantauan jarak jauh, diagnostik, manajemen energi, dan sistem transportasi.
Ethernet vs. Modbus: Mana yang Harus Anda Pilih?
Kebutuhan Transmisi Data dan Kinerja Real-Time
Pilih Ethernet jika sistem Anda memerlukan transfer data berkecepatan tinggi dan kontrol waktu nyata, seperti dalam sistem kontrol gerak multi-sumbu.Kompleksitas Sistem dan Jumlah Perangkat
Untuk jaringan sederhana dengan lebih sedikit perangkat, Modbus menawarkan solusi yang terjangkau dan mudah diterapkan.Kompatibilitas dan Integrasi
Jika Anda membutuhkan interoperabilitas dengan berbagai perangkat vendor dan integrasi yang mulus dengan sistem TI, Ethernet (terutama EtherNet/IP) adalah pilihan yang lebih baik.Lingkungan dan Jarak Transmisi
Ethernet berfungsi dengan baik di lingkungan kabel yang stabil. Namun, Modbus RTU lebih baik daripada RS-485 untuk jarak jauh dan kondisi yang keras, seperti lingkungan dengan gangguan elektromagnetik.Biaya dan Skalabilitas
Ethernet ideal untuk sistem berskala besar yang dapat diperluas, meskipun biaya awalnya lebih tinggi. Sebaliknya, Modbus menawarkan opsi berbiaya rendah untuk sistem yang lebih kecil atau lama.
Pertanyaan Umum tentang Modbus dan Ethernet
1. Apakah Ethernet lebih cepat dari Modbus?
Ya, Ethernet menawarkan kecepatan transmisi yang jauh lebih tinggi, mendukung hingga 1 Gbps atau lebih, sementara Modbus RTU biasanya beroperasi antara 9600 dan 115200 bps. Ethernet lebih cocok untuk aplikasi yang membutuhkan throughput data tinggi dan respons waktu nyata.
2. Apa perbedaan antara Modbus serial dan Ethernet?
Modbus serial (misalnya, RS-232, RS-485) menggunakan komunikasi serial untuk koneksi jarak pendek dan kecepatan data yang lebih rendah. Ethernet mendukung kecepatan yang lebih tinggi dan jarak yang lebih jauh melalui jaringan TCP/IP, sehingga lebih baik untuk pemantauan jarak jauh dan jaringan yang kompleks.
3. Dapatkah kabel Ethernet digunakan untuk Modbus?
Ya, Modbus TCP/IP berjalan melalui jaringan Ethernet, yang memungkinkan kabel Ethernet untuk menghubungkan perangkat yang kompatibel dengan Modbus. Kombinasi ini memanfaatkan kesederhanaan Modbus dengan kecepatan dan fleksibilitas Ethernet, ideal untuk sistem otomasi industri yang memerlukan pemantauan jarak jauh.
4. Apa perbedaan antara Ethernet dan Profibus?
Ethernet adalah standar terbuka yang digunakan di seluruh lingkungan TI dan industri, yang mendukung transfer data berkecepatan tinggi dan kontrol waktu nyata. Di sisi lain, Profibus adalah fieldbus khusus yang berfokus pada otomatisasi proses. Sementara Profibus menawarkan determinisme yang lebih baik, Ethernet lebih fleksibel dan lebih mudah diintegrasikan dengan sistem TI dan IIoT modern.
Dukung proyek Anda dengan PLC Omron, Mitsubishi, Schneider baru dan asli – tersedia sekarang!
Kesimpulan
Singkatnya, jika aplikasi Anda memerlukan transmisi data berkecepatan tinggi dan real-time, Ethernet (terutama EtherNet/IP) adalah pilihan terbaik Anda. Untuk jaringan sensor dan sistem kontrol yang lebih sederhana, Modbus tetap menjadi solusi yang andal dan hemat biaya.
Apa pun protokol yang Anda pilih, penting untuk memastikan pemasok Anda menyediakan peralatan baru dan asli dengan pengiriman cepat. Di Kwoco, kami memahami bahwa pengiriman tepat waktu dan kualitas produk adalah kunci untuk membangun kepercayaan pelanggan. Ada pertanyaan? Jangan ragu untuk menghubungi saya di [email protected].
Hubungi kami
Cukup isi nama, alamat email, dan deskripsi singkat pertanyaan Anda dalam formulir ini. Kami akan menghubungi Anda dalam waktu 24 jam.
Kategori Produk
Produk Penjualan Panas
Anda Mungkin Juga Menemukan Topik Ini Menarik
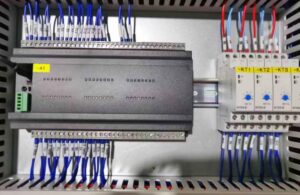
PLC Keamanan vs. PLC Standar: Panduan Teknisi
Dalam lingkungan komersial yang sangat otomatis saat ini, Pengontrol Logika Terprogram (PLC) berperan sebagai "otak" inti yang menggerakkan manufaktur. Namun, banyak pengambil keputusan dan perancang kesulitan membedakan antara PLC konvensional dan PLC Keamanan, karena gagal memahami sepenuhnya perbedaan mendasar dalam filosofi desain, aplikasi fungsional, dan jaminan keamanannya.
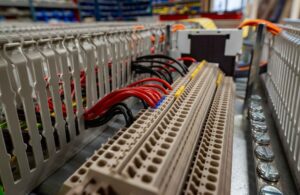
24VDC vs 120VAC: Memahami Perbedaan dalam Otomasi
Saat memilih tegangan kontrol untuk otomasi industri, dua pilihan umum adalah 24VDC dan 120VAC. Namun, bagaimana Anda memutuskan mana yang tepat untuk aplikasi Anda? Dalam artikel ini, kami akan menguraikan perbedaan utama antara 24VDC dan 120VAC, mengeksplorasi kegunaannya dalam sistem otomasi, dan membantu Anda membuat keputusan yang tepat berdasarkan kebutuhan Anda.
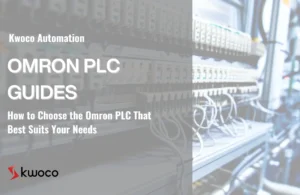
Cara Memilih PLC Omron yang Paling Sesuai dengan Kebutuhan Anda
Cara Memilih PLC Omron yang Paling Sesuai dengan Kebutuhan Anda Berjuang untuk menemukan PLC yang tepat untuk industri Anda