Útmutató a PLC analóg I/O-hoz automatizálási mérnökök számára
Ha Ön automatizálási mérnök, ez a cikk megadja azokat az alapvető ismereteket, amelyekre szüksége van ahhoz, hogy magabiztosan dolgozhasson az analóg jelekkel PLC környezet. Ennek az olvasmánynak a végére jobban megérti a feszültséget és áramerősséget, az analóg bemenetekkel való megfelelő interfészeket, és hogyan optimalizálhatja rendszereit a jobb teljesítmény érdekében.
Tehát nézzük meg, hogyan javíthatja munkafolyamatát és hatékonyságát a PLC analóg bemeneti és kimeneti rendszerek elsajátításával.
Tartalomjegyzék
Mi az analóg bemenet a PLC rendszerekben?
Az analóg bemenet folyamatos jelek (általában feszültség vagy áram) fogadásának folyamata külső eszközökről, mint pl érzékelők, amely valós változókat jelenthet, például hőmérsékletet, nyomást vagy szintet. A PLC rendszerben ezek a bemenetek elengedhetetlenek az ipari folyamatok felügyeletéhez és vezérléséhez.
A PLC analóg bemeneti modulja felelős a bejövő analóg jelek digitális adatokká alakításáért, amelyeket a PLC képes feldolgozni.
Analóg jelek típusai
Az analóg bemenetek lehetnek feszültség vagy áram formájában. Az általános feszültségszintek közé tartozik a 0-5 V, 0-10 V vagy 4-20 mA, míg az áramjelek általában 4-20 mA között mozognak. Ezek a jelek folyamatosan változnak, ellentétben a be- vagy kikapcsolt digitális jelekkel. Ezeknek a jeleknek a megfelelő átalakítása kulcsfontosságú a rendszer pontos teljesítményéhez.
Kulcsfontosságú komponensek
A PLC-ben lévő bemeneti kártyát jellemzően egy meghatározott típusú analóg bemenet kezelésére tervezték (feszültség vagy áram). Az analóg bemeneti modul kritikus szerepet játszik azáltal, hogy a jelet a PLC-rendszer által értelmezhető formába alakítja. Ez az átalakítás lehetővé teszi az automatizálási rendszer számára, hogy valós bemenetek alapján adatvezérelt döntéseket hozzon.
2. Hogyan befolyásolja a feszültség és az áram a PLC analóg bemeneteit?
Alapvető fontosságú annak megértése, hogy a feszültség és az áram hogyan hatnak egymásra a PLC rendszerrel. Mind a feszültség, mind az áramjelek különböző érzékelőkkel kommunikálnak, és olyan bemeneti adatokat szolgáltatnak, amelyek szabályozhatják a műveleteket, például a sebességet, a hőmérsékletet és a nyomást.
De miért kritikus a feszültség és az áramerősség, és hogyan befolyásolják a PLC analóg bemeneti rendszerének működését?
A feszültség hatása
A feszültségjeleket általában olyan helyzetekben használják, amikor fizikai mennyiség mérésére van szükség. Például a hőmérséklet-érzékelők (például RTD-k és hőelemek) gyakran feszültségjeleket adnak ki.
Ezek az érzékelők feszültségtartományban (pl. 0-5V, 0-10V) küldenek adatokat, amelyeket a PLC bemenetnek pontosan kell értelmeznie a megfelelő folyamatvezérlés érdekében.
Az áram szerepe
Másrészt az áramjelek (általában 4-20 mA) robusztusabbak zajos ipari környezetben. Az áram általában kevésbé érzékeny a feszültségesésre nagy távolságokon, így ideális olyan alkalmazásokhoz, ahol kritikus a pontos adatátvitel.
Például, amikor nyomásérzékelőkkel vagy áramlásmérőkkel dolgozik, az áramjelek megbízható adatokat szolgáltatnak a PLC-rendszer feldolgozásához.
Mi az érzékelők szerepe az analóg bemeneti és kimeneti rendszerekben?
Az érzékelők képezik az analóg bemeneti és kimeneti rendszerek gerincét. Valós adatokat gyűjtenek, és azokat a PLC által megérthető jellé alakítják át. Az érzékelők, például a hőmérséklet-érzékelők, mérőcellák és nyomáskapcsolók szerves részét képezik az automatizálási rendszerek működéséhez szükséges környezeti adatok rögzítésének.
A PLC rendszerekben használt érzékelők típusai
Az analóg érzékelők gyakori típusai közé tartoznak az RTD-k, hőelemek és mérőcellák, amelyek mindegyike egyedi típusú jelet ad a PLC-nek. Például az RTD-k olyan ellenállásértéket adnak ki, amely feszültségjellé alakítható át PLC analóg bemenetéhez, míg a terhelésmérő cellák analóg jellé konvertálják a nyúlásmérő méréseket.
Kihívások érzékelőkkel
Ha analóg érzékelőkkel dolgozik, gondoskodni kell arról, hogy az érzékelő megfelelően legyen kalibrálva a pontos leolvasás érdekében. A vezetékek és az árnyékolás szintén fontosak a zaj és az interferenciák csökkentése érdekében, amelyek befolyásolhatják a PLC-rendszerbe küldött analóg jelek integritását.
Hogyan lehet elhárítani az analóg bemeneti problémákat a PLC rendszerekben?
Automatizálási környezetben az analóg bemeneti problémákat számos tényező okozhatja, például rossz vezetékezés, jelromlás vagy a PLC analóg bemeneti moduljával kapcsolatos problémák. Ezeknek a problémáknak a hatékony elhárítása kulcsfontosságú a rendszer optimális teljesítményének biztosításához.
Gyakori hibaelhárítási lépések
- Ellenőrizze a vezetékek csatlakozásait: A laza vagy hibás vezetékek jelveszteséghez vagy hibás leolvasásokhoz vezethetnek. Győződjön meg arról, hogy minden csatlakozás biztonságos és megfelelően árnyékolt.
- Ellenőrizze a jelskálázást: Ha az érzékelő kimeneti jele nem egyezik a várt tartománnyal, előfordulhat, hogy a bemenetet a PLC konfigurációs beállításaiban kell skálázni.
- Figyelje a jel integritását: Használjon voltmérőt vagy oszcilloszkópot annak ellenőrzésére, hogy az analóg bemenet egyezik-e a várt értékekkel. A feszültségeséssel vagy áramszivárgással kapcsolatos problémák hibás leolvasást okozhatnak.
Speciális hibaelhárító eszközök
Bonyolultabb problémák esetén az automatizálási mérnökök fejlett diagnosztikai eszközöket, például jelátalakítókat vagy analóg-digitális átalakítókat (ADC) használhatnak a PLC analóg bemeneti rendszerének problémáinak azonosítására. Ezek az eszközök segíthetnek a feszültség- vagy áramjel kalibrálásával kapcsolatos problémák pontos meghatározásában.
Melyek a legjobb gyakorlatok az analóg bemenetek skálázására az automatizálásban?
Ha nagyméretű automatizálási rendszerekkel foglalkozunk, az analóg bemenetek hatékony skálázása kulcsfontosságú. Akár több érzékelőt kezel, akár nagy pontosságú berendezésekkel dolgozik, a megfelelő méretezés biztosítja, hogy a PLC nagyszámú bemenetet tud kezelni a teljesítmény feláldozása nélkül.
Tippek az analóg bemenetek skálázásához
- Több bemeneti modul használata: Ha nagyszámú analóg bemenetet kezel, gyakran a legjobb, ha több PLC bemeneti modult használ. Ez lehetővé teszi a terhelés jobb elosztását, és biztosítja, hogy az analóg bemeneti modulok ne legyenek túlterhelve.
- Jelkondicionálás használata: A jelkondicionálási technikák, például a feszültségosztók és erősítők segítenek a jelek skálázásában és beállításában a pontos feldolgozás érdekében. Ez különösen akkor hasznos, ha alacsony feszültségű jeleket kezel.
- Vegye figyelembe a bemeneti ellenállást: A különböző típusú analóg bemeneti modulok eltérő bemeneti ellenállással rendelkeznek. Annak biztosítása, hogy a PLC-rendszer kompatibilis-e az érzékelő ellenállásával, elengedhetetlen a pontos leolvasások biztosításához.
Gyakran Ismételt Kérdések
Mi a különbség a feszültség és az áramerősség között az analóg bemeneteken?
A feszültségjelek folyamatos mérések, amelyeket általában olyan érzékelőknél használnak, mint a hőelemek, míg az áramjeleket kevésbé befolyásolja a távolság, és ideálisak olyan érzékelőkhöz, mint a nyomáskapcsolók vagy az áramlásmérők.
Hogyan kalibrálhatok egy PLC analóg bemeneti modult?
A kalibrálás általában magában foglalja a bemeneti skálázás beállítását a PLC konfigurációban, hogy megfeleljen a csatlakoztatott érzékelő vagy adó várható tartományának.
Miért ingadozik az analóg jelem?
Az ingadozást számos tényező okozhatja, beleértve a laza csatlakozásokat, az interferenciát vagy a vezetékek nem megfelelő árnyékolását. Mindig gondoskodjon a megfelelő földelésről és árnyékolásról a vezetékekben.
Hogyan skálázhatok egy 4-20 mA áram bemeneti jelet?
A 4-20 mA árambemenet skálázása magában foglalja az áramértékek megfelelő folyamatváltozó tartományba való konvertálását, gyakran jelkondicionáló segítségével vagy a skálázás beállításával a PLC rendszerben.
Erősítse meg projektjeit vadonatúj, eredeti Omron, Mitsubishi, Schneider PLC segítségével – raktáron, készen áll!
Következtetés
- Az analóg bemeneti és kimeneti jelek kulcsfontosságúak az ipari folyamatok automatizálásában, és két fő formában jelennek meg: feszültség és áram.
- A megfelelő kalibrálás és jelkondicionálás kulcsfontosságú az érzékelők és a PLC rendszer közötti pontos adatátvitelhez.
- Az analóg bemenettel kapcsolatos problémák elhárítása magában foglalja a vezetékezési hibák ellenőrzését, a jel integritásának ellenőrzését és a megfelelő skálázás biztosítását.
- Az analóg bemenetek hatékony skálázása nagy rendszerekben elengedhetetlen a több érzékelő kezeléséhez és a túlterhelés elkerüléséhez.
A PLC analóg bemenetek és kimenetek alapvető fogalmainak megértésével javíthatja automatizálási rendszereinek megbízhatóságát és pontosságát, növelve a projektek működési hatékonyságát.
Új, eredeti PLC-ket keres projektjeihez? A Kwoco-nál a legfrissebb PLC-ket kínáljuk olyan legnépszerűbb márkáktól, mint például Omron, Mitsubishi, és Schneider. Vásároljon bizalommal – gyors szállítás, garantált minőség! Vásároljon most
Lépjen kapcsolatba velünk
Csak töltse ki nevét, e-mail címét és kérésének rövid leírását ezen az űrlapon. 24 órán belül felvesszük Önnel a kapcsolatot.
Ezeket a témákat is érdekesnek találhatja
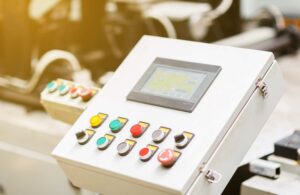
PLC számlálóprogramozás: Teljes útmutató az automatizáláshoz 2024
Szeretne mélyen megérteni a PLC-számláló programozását? Akár tapasztalt programozó, akár csak most kezdi a PLC-ket, ez az átfogó útmutató végigvezeti Önt mindenen, amit tudnia kell a számlálóutasításokról és azok gyakorlati alkalmazásáról az ipari automatizálásban.
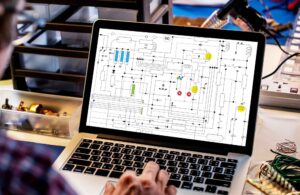
Alapvető útmutató a PLC hibákhoz és hibaelhárítási technikákhoz
A programozható logikai vezérlők (PLC) létfontosságúak a modern automatizálási rendszerekben, és számtalan ipari folyamat gerincét szolgálják. Szerepük a gépek kezelésében és a rendszerek koordinálásában nélkülözhetetlen. Azonban, mint minden technológia, a PLC-k is ki vannak téve idővel hibáknak és meghibásodásoknak.
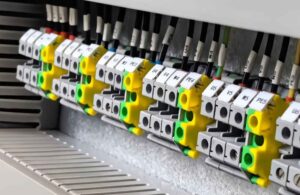
Kontaktor vs relé: A kontaktorok és a relék közötti különbség megértése
Ez a cikk mélyen belemerül a kontaktorok és relék világába, amelyek az ipari automatizálási és vezérlőrendszerek két alapvető összetevője. Feltérképezzük funkcióikat, különbségeiket és alkalmazásaikat, segítve annak megértését, hogy ez az információ miért létfontosságú a gép- és berendezésgyárakban, a gyártásban vagy a gyári megoldásokat gyártó cégekben részt vevő személyek számára. Akár meglévő elektromos rendszerét szeretné optimalizálni, akár újat tervezni, a relé és a kontaktor közötti árnyalatok megértése jelentősen befolyásolhatja a hatékonyságot, a biztonságot és a költséghatékonyságot.